Advanced Tips for Troubleshooting Pressurisation Units in Commercial Buildings
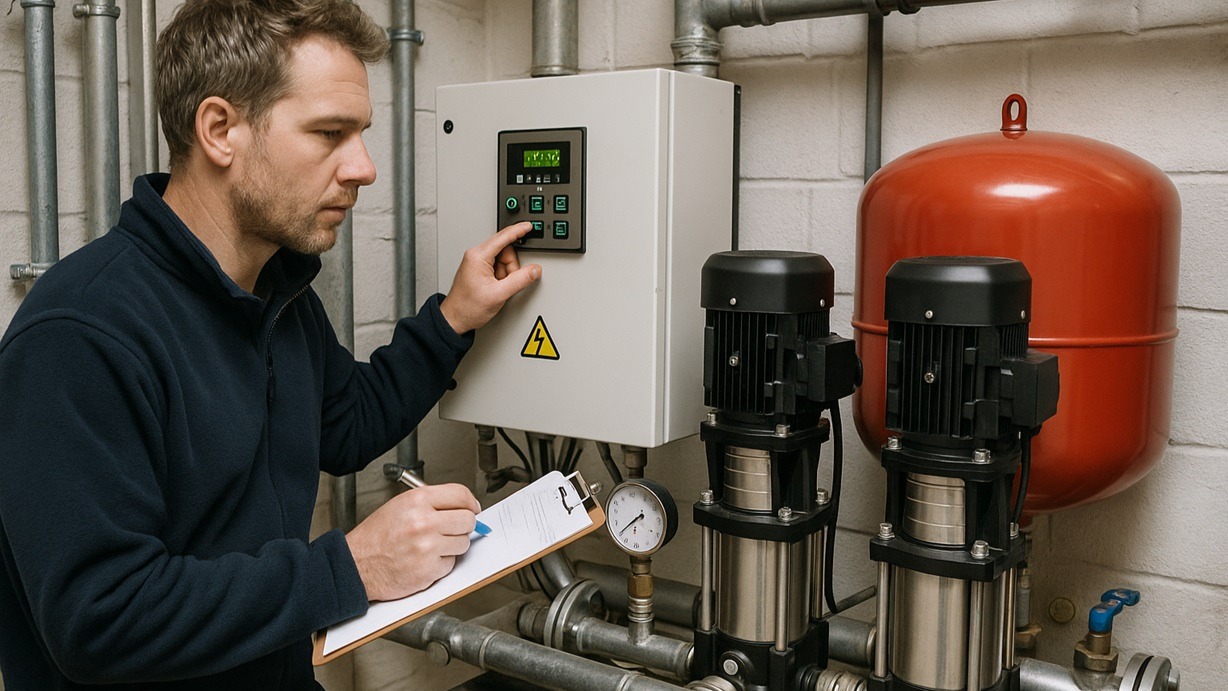
Maintaining the seamless operation of a commercial building's heating system is paramount for ensuring a comfortable and productive environment. At the heart of this system lies the pressurisation unit, a critical component responsible for maintaining the precise pressure required for efficient heat distribution. While routine maintenance can often prevent common issues, complex problems can arise, demanding a more advanced approach to troubleshooting pressurisation units. This comprehensive guide will delve into sophisticated techniques and strategies to help you effectively diagnose and resolve intricate problems, ensuring your heating system operates reliably and efficiently.
Reaffirming the Fundamentals: The Role of Pressurisation Units
Before we delve into advanced troubleshooting pressurisation units, it's beneficial to reiterate the fundamental function of these vital components briefly. Pressurisation units are integral to closed-loop heating systems, primarily maintaining a consistent and optimal pressure level. This ensures that the heated water circulates effectively throughout the building, preventing pressure drops that can lead to cold spots, inefficient heating, and potential system failures. Recognising deviations from normal operation, such as fluctuating pressure, unusual noises, or water leaks, is the first step in identifying potential pressurisation unit issues.
Laying the Groundwork for Advanced Troubleshooting
Effective troubleshooting pressurisation units requires meticulous preparation and a commitment to safety.
Prioritising Safety: A Non-Negotiable First Step
Safety must always be the paramount concern when undertaking any maintenance or troubleshooting on a commercial heating system. Before commencing any diagnostic procedures, it is absolutely essential to completely shut down the system and isolate the pressurisation unit from the power supply. Furthermore, ensure that you are equipped with the appropriate personal protective equipment (PPE), including safety glasses, gloves, and any other recommended gear. This seemingly precautionary step can prevent serious accidents and should never be overlooked.
Assembling the Essential Toolkit for Advanced Diagnostics
Having the right tools readily available is crucial for efficient and accurate troubleshooting pressurisation units. Beyond basic hand tools, consider the following:
- Calibrated Pressure Gauge: A reliable pressure gauge is essential for accurately measuring system pressure at various points.
- Multimeter: This versatile tool is invaluable for testing the electrical components of the pressurisation unit, such as sensors and pump motors.
- Infrared Thermometer: This can help identify temperature anomalies that might indicate blockages or overheating components.
- Flow Meter (if applicable): For systems with flow monitoring capabilities, a flow meter can help diagnose circulation issues.
- System Bleeding Key: Essential for effectively removing trapped air from the heating system.
Leveraging Documentation: Your Informational Arsenal
Never underestimate the value of your unit's technical manual and meticulously maintained maintenance logs. These documents often contain detailed specifications, wiring diagrams, troubleshooting guides specific to your model, and records of past issues and their resolutions. Familiarising yourself with this information can provide crucial insights and significantly expedite the fixing pressurisation units process.
Advanced Techniques for Diagnosing Pressurisation Unit Issues
Moving beyond basic checks, let's explore advanced techniques for pinpointing the root causes of common pressurisation unit issues.
Deeper Dive into Diagnosing Pressure Fluctuations
Persistent or erratic pressure fluctuations require a more in-depth investigation beyond simple sensor recalibration and system bleeding.
- Advanced Sensor Diagnostics: Use a multimeter to test the resistance or voltage output of the pressure sensor across its operating range. Compare these readings against the manufacturer's specifications to identify any inconsistencies or drift. A faulty sensor may provide intermittent or inaccurate readings, leading to unstable pressure control.
- Expansion Vessel Analysis: The expansion vessel plays a critical role in absorbing pressure changes due to water volume fluctuations. Isolate the expansion vessel and check its pre-charge pressure. A loss of pre-charge or a damaged internal bladder can lead to rapid pressure fluctuations. Recharging or replacing the expansion vessel may be necessary. Refer to our range of Expansion Vessels.
- System Component Cycling Analysis: Observe the frequency and duration of the pressurisation pump's operation. Excessive cycling might indicate a small leak in the system that the unit is constantly trying to compensate for, or it could point to an incorrectly sized expansion vessel.
Pinpointing the Source of Noisy Operation: Advanced Diagnostics
Persistent or unusual noises warrant a detailed investigation to prevent potential component damage.
- Detailed Cavitation Analysis: Beyond checking for simple blockages, assess the Net Positive Suction Head Available (NPSHa) and Net Positive Suction Head Required (NPSHr) for your pump. Insufficient NPSHa can lead to cavitation, even without obvious blockages. Ensure proper pipe sizing and pump placement.
- Vibration Analysis: Use vibration monitoring equipment to identify specific frequencies that might indicate failing pump bearings or impeller imbalance. Addressing these issues early can prevent catastrophic pump failure. Explore our selection of reliable pumps from Grundfos and Wilo.
- Flow Restriction Identification: Partially blocked pipes, clogged strainers, or malfunctioning valves can create turbulent flow and noise. Use pressure differential readings across components to identify restrictions.
Advanced Techniques for Resolving Water Leaks
Locating and fixing pressurisation units with persistent leaks often requires a systematic approach.
- Pressure Testing in Isolated Sections: Isolate different sections of the heating system and perform pressure tests to pinpoint the location of less obvious leaks. A slow pressure drop in a specific section indicates a leak within that area.
- Thermal Imaging: A thermal imaging camera can be invaluable for identifying subtle leaks, especially in concealed pipework, by detecting temperature anomalies caused by escaping water.
- Ultrasonic Leak Detection: This technology can detect the high-frequency sounds produced by escaping fluids, even in noisy environments, allowing for precise leak location.
Addressing Complex System Filling Issues
When a pressurisation unit struggles to maintain pressure due to filling problems, advanced diagnostics are needed.
- Flow Rate Measurement of Filling System: Measure the flow rate of the water supply to the pressurisation unit to ensure it meets the system's requirements. A restricted flow could indicate a blockage or a faulty filling valve.
- Non-Return Valve Inspection: Malfunctioning non-return valves in the filling line can prevent proper filling or allow backflow. Carefully inspect these valves for proper operation.
- Automatic Filling Valve Diagnostics: Test the functionality of the automatic filling valve using a multimeter to check for proper electrical signals and mechanical operation. A faulty valve may need replacement.
Leveraging Technology for Enhanced Troubleshooting and Monitoring
Modern technology offers powerful tools for troubleshooting pressurisation units and proactively managing heating system performance.
Real-Time Digital Monitoring Systems
Implementing a digital monitoring system provides continuous real-time data on system pressure, pump operation, and other critical parameters. This allows for immediate detection of anomalies and can often provide early warnings of potential pressurisation unit issues before they lead to significant problems.
Data Logging and Trend Analysis
Data logging capabilities allow you to track system performance over extended periods. Analysing these trends can reveal subtle deviations from normal operation that might not be apparent in real-time readings. This historical data is invaluable for identifying recurring issues and predicting potential failures.
Remote Monitoring and Control Solutions
Remote monitoring systems enable you to access real-time and historical data from your pressurisation unit from anywhere with an internet connection. Some advanced systems also allow for remote adjustments to system parameters, facilitating proactive fixing pressurisation units and optimising performance.
Knowing When to Call the Experts: Recognising Your Limitations
While advanced DIY troubleshooting pressurisation units can resolve many issues, certain situations demand the expertise of qualified professionals.
- Complex Electrical Faults: Diagnosing and repairing intricate electrical problems within the pressurisation unit's control system should be left to experienced technicians.
- Refrigerant Leaks (in some combined units): If your pressurisation unit is part of a combined heating and cooling system, refrigerant leaks require specialised equipment and expertise.
- Unfamiliar or Recurring Issues: If you encounter problems that you cannot confidently diagnose or if the same issues repeatedly arise, seeking professional help is the most prudent course of action.
Proactive Strategies for Minimising Future Pressurisation Unit Issues
Preventing problems is always more efficient than fixing pressurisation units after they occur. Implementing proactive measures is key.
Establishing Comprehensive Regular Maintenance Routines
A well-defined and consistently followed maintenance schedule is the cornerstone of preventing pressurisation unit issues. This should include regular inspections, thorough cleaning of components, accurate sensor calibrations, and timely replacement of wear-prone parts.
Investing in Comprehensive Staff Training
Empowering your maintenance staff with a thorough understanding of the pressurisation unit's operation, common failure modes, and basic troubleshooting pressurisation units procedures can significantly improve early detection and prevent minor issues from escalating.
National Pumps and Boilers: Your Partner in Advanced Troubleshooting Support
At National Pumps and Boilers, we possess the advanced expertise and diagnostic tools necessary to tackle even the most complex pressurisation unit issues in commercial buildings. Our experienced team is equipped to provide comprehensive troubleshooting support, from in-depth diagnostics to efficient repair and replacement services. We understand the critical role these units play in maintaining a comfortable and productive environment, and we are committed to ensuring your heating system operates reliably and efficiently. Contact us for expert assistance with fixing pressurisation units and maintaining optimal system performance. We offer support for a wide range of brands, including Remeha and Vaillant.
Taking a Proactive Approach to Pressurisation Unit Health
Effectively troubleshooting pressurisation units requires a blend of technical knowledge, systematic investigation, and the appropriate tools. By understanding advanced diagnostic techniques, leveraging modern technology, and knowing when to seek professional support from partners like National Pumps and Boilers, you can minimise downtime, ensure the efficient operation of your commercial heating system, and create a comfortable environment for all occupants. Don't wait for a minor issue to become a major disruption – take a proactive approach to the health of your pressurisation unit today. Reach out to us via our Contact Page to discuss your specific needs and learn how we can help you maintain a reliable and efficient heating system. Explore our range of Commercial Circulators and Pump Valves for optimal system integration.