Common Central Heating Issues and How to Troubleshoot Them
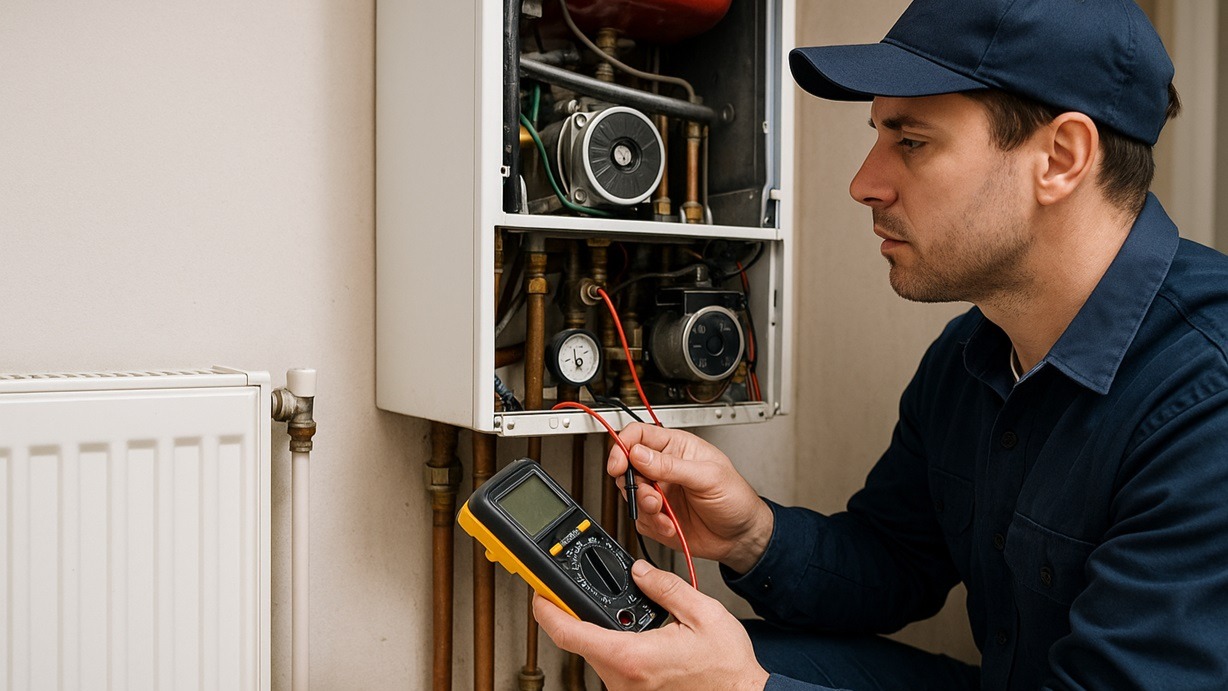
A reliable commercial central heating system is the backbone of any business, ensuring offices, warehouses, and retail spaces remain comfortable year-round. However, even the best installations can encounter central heating issues, leading to increased costs, downtime and unhappy occupants. With a little know-how in heating troubleshooting, many common faults can be identified and often resolved without waiting for an engineer. Below, we explore frequent problems, their causes and practical steps you can take before calling in the professionals.
Uneven Heating Across the Building
Why It Happens
Uneven temperatures, sauna-like boardrooms next to freezing corridors, are a common gripe in large properties. Causes include:
- Air Trapped in Radiators: Air pockets prevent hot water from circulating properly.
- Imbalanced Flow: Some radiators may receive more water flow than others.
- Thermostat Zoning Faults: Incorrectly calibrated thermostats can starve or overheat certain zones.
Heating Troubleshooting Steps
- Bleed Radiators
Use a radiator key on the bleed valve to release trapped air until water flows steadily. - Check Thermostat Settings
Inspect each zone’s control and ensure setpoints correspond to occupied areas, offices, meeting rooms, and storage. - Balance the System
Adjust lockshield valves to redistribute flow evenly. For larger systems, call us to perform a full hydraulic balance.
For replacement radiator valves or to upgrade thermostatic controls, explore our pump-valves and pressurisation-units categories.
Boiler Not Turning On
Likely Causes
A boiler refusing to fire up is an immediate concern. Possible culprits include:
- Thermostat Fault: Dead batteries or misconfiguration.
- Power Supply Issues: Tripped breakers or faulty electrical connections.
- Low System Pressure: Below the minimum threshold, boilers will lock out.
Heating Troubleshooting Steps
- Thermostat Check
Replace batteries, reset settings or swap to a spare unit. - Electrical Supply
Verify the boiler’s isolator switch is on and check your fuse board for tripped circuits. - Re-pressurise the System
Using the filling loop, top up pressure to around 1.2 bar (refer to your boiler manual).
If the boiler still won’t ignite, it may be the pilot light, ignition electrode or internal safety cut-offs. It's time to call our Gas Safe engineers via our contact page.
Radiators Not Heating Properly
What’s Going On?
Cold spots at the top of a radiator or completely cold panels usually indicate:
- Air Locks: Trapped air disrupts circulation.
- Sludge Build-Up: Corrosion debris accumulating in older systems.
Heating Troubleshooting Steps
- Bleeding
As above, bleed radiators to expel air. - Powerflush Consideration
Persistent cold areas often require a professional power flush to remove sludge. We recommend our full system flush service with magnetic filters from Mikrofill or Flamco.
Strange Noises from Boilers or Pipes
Common Noises and Causes
- Gurgling: Air in the system.
- Banging/Kettling: Limescale inside the heat exchanger is causing localised boiling.
- Whistling: High flow rates or partially closed valves.
Heating Troubleshooting Steps
- Bleed the System
Remove air to silence gurgles. - Check System Pressure
Low pressure can cause cavitation noises; re-pressurise as needed. - Descale or Service
Kettling requires descaling by professionals. Book our maintenance team for a boiler service, including descaling and valve checks.
Leaking or Dripping From the Boiler
Possible Faults
Leaks can stem from loose fittings, failed seals or a faulty pressure-relief valve.
Heating Troubleshooting Steps
- Tighten Connections
Use spanners to nip up any loose pipework joints. - Inspect Relief Valve
A leaking valve often signals overpressure. Adjust the filling loop or contact us for valve replacement. - Professional Assessment
Corrosion inside the boiler casing or heat exchanger requires expert repair. Reach out on our contact page.
Boiler Losing Pressure
Why It Matters
Frequent pressure drops force repeated top-ups and can indicate an underlying leak or component failure.
Heating Troubleshooting Steps
- Visual Leak Check
Inspect radiators, pipe joints and the boiler itself for drips. - Check Pressure-Relief Valve
A faulty PRV may need replacement. - Call for Leak Detection
Hidden leaks warrant a specialist leak-detection service. Ask about our submersible pumps and pipe diagnostics.
Thermostat and Control Issues
Symptoms
Erratic heating, failure to respond or constant cycling often trace back to faulty controls.
Heating Troubleshooting Steps
- Battery and Calibration
Swap batteries and recalibrate your thermostat. - Relocate if Necessary
Move the sensor away from drafts, heat sources or direct sunlight. - Upgrade Controls
Consider programmable or smart thermostats for better zoning and energy insights. Explore our central-heating services for full control system upgrades.
Pump Failures and No Flow
Indicators
Cold radiators despite boiler operation, or a boiler lock-out due to no flow.
Heating Troubleshooting Steps
- Pump Examination
Check circulator pumps from Grundfos, Wilo or DAB for hums or blockages. - Valve Position
Ensure all zone valves are open. - Professional Pump Service
If pumps stall, we offer repair and replacement for all major brands, including Lowara and Armstrong.
Expansion Vessel and Pressure Relief
Why They Matter
A faulty expansion vessel leads to pressure spikes and frequent leaks. The pressure-relief valve then activates, releasing water to protect the system.
Heating Troubleshooting Steps
- Check Vessel Charge
A workshop air-pressure gauge can confirm if the vessel needs recharging. - Replace Worn Components
We stock expansion vessels and PRVS for immediate replacement.
Preventative Maintenance: The Best Troubleshooter
Routine servicing is the single most effective form of heating troubleshooting, catching small issues before they escalate into costly breakdowns. Our annual maintenance plans include:
- Boiler health checks (brands: Vaillant, Remeha, Hamworthy)
- Pipework and joint inspections
- Pump servicing and flow-rate optimisation
- System flushing and filter replacement with Mikrofill magnetic filters
- Thermostat calibration and control-system health review
Frozen Pipes and Condensate Issues
In colder months, a common culprit behind sudden heat loss is a frozen condensate pipe or networked pipework. Commercial boilers expel acidic condensate, which can freeze in external pipes if they aren’t properly lagged.
Troubleshooting steps:
- Inspect external condensate run: Look for frost or ice build-ups on plastic discharge pipes.
- Carefully thaw: Pour warm (not boiling) water over the pipe section, or wrap it in a heated towel. Never use a naked flame.
- Improve insulation: Once thawed, apply lagging or install trace heating cables to prevent recurrence.
If you suspect internal pipework frost, particularly in unheated plant rooms or lofts, contact us for a survey and ask about our submersible pumps solutions to help keep water moving through vulnerable circuits.
Corrosion, Inhibitors and Water Treatment
Sludge isn’t the only enemy lurking in your system; corrosion can eat away at heat exchangers and pipework fittings, leading to leaks or component failure.
Key preventative measures:
- Chemical inhibitors: Adding a high-performance inhibitor (such as those from our Mikrofill range) helps protect metal surfaces and prolongs equipment life.
- Magnetic filters: Install a filter in the pump return line to capture ferrous particles. Our Flamco magnetic filters are ideal for commercial systems.
- Regular water quality checks: Annual sampling for ph and conductivity ensures early detection of corrosive water conditions.
For a full chemical treatment and filter installation, browse our expansion vessels and inhibitor services.
Digital Fault Codes and Diagnostics
Modern commercial boilers and control panels display fault codes when something goes awry, ranging from ignition failures to sensor faults. Understanding these codes can speed up resolution.
- Common codes:
- E01/E02: Flame loss or ignition lockout.
- F22: Low water pressure lockout.
- F75: Condensate blockage.
What you can do:
- Consult the manual: Each brand, be it Vaillant, Remeha or Hamworthy, has a troubleshooting guide for fault codes.
- Reset safely: Many boilers allow a simple reset sequence via the front panel; only attempt this if you’re confident.
- Log and report: Note the code and operating conditions when calling an engineer via our contact page to help them diagnose remotely.
Remote Monitoring and Predictive Maintenance
For larger estates or multi-site operations, remote monitoring can transform heating troubleshooting from reactive to proactive:
- Data logging: Trend logs of flow temperatures, pressure, and burner cycles highlight gradual performance drifts.
- Alerts: Instant notifications via email or SMS when a parameter goes outside acceptable limits, no more after-hours surprises.
- Cloud platforms: Integrate with BMS (BACnet/Modbus) to view all HVAC data on a single dashboard.
Our experts can install smart controllers compatible with Stuart Turner and NPB thermostats, ensuring you stay ahead of potential faults.
Case Study: Rapid Response Saves the Day
A large retail outlet in Birmingham experienced frequent boiler lockouts (code F22) during peak trading hours, forcing temporary closures of customer toilets due to a lack of hot water. After initial heating troubleshooting, our engineers discovered:
- Pressure creep caused by a failing expansion vessel.
- Blocked condensate trap from limescale buildup.
Within hours, we fitted a replacement expansion vessel, descaled the condensate trap and recalibrated the control panel. The store reopened the same evening, saving thousands in lost sales.
Preventative Best Practices
To minimise future central heating issues:
- Scheduled servicing: Annual checks by Gas Safe engineers, including burner clean, flue integrity and safety device testing.
- Temperature profiling: Use portable dataloggers to map hot and cold spots before they become complaints.
- Staff training: Show on-site teams simple tasks, bleeding radiators, resetting boilers, and checking fuel levels.
Pair routine checks with parts from our commercial circulators and DHW pumps to keep every component in prime condition.
By expanding your toolkit with these advanced heating troubleshooting techniques, alongside regular maintenance and smart monitoring, you’ll reduce downtime, extend equipment life and keep your commercial premises warm and productive. For expert support, system upgrades or tailored maintenance plans, visit our homepage or contact us today.
When to Call a Professional
While many issues can be tackled in-house, always err on the side of safety if you encounter:
- Gas leaks or smell of gas
- Electrical faults or frequent breaker trips
- Major water leaks or boiler corrosion
- Persistent pressure problems despite bleeding and repressurising
- Complex control-system failures
For all emergency and planned work, trust the Gas Safe–registered engineers at National Pumps and Boilers. We offer 24/7 support. Book a call via our contact page.
By familiarising yourself with these central heating issues and proactive heating troubleshooting techniques, you can reduce downtime, avoid unnecessary costs and ensure your commercial heating system delivers reliable warmth throughout the year. For comprehensive diagnostics, repairs or system upgrades, visit our homepage or reach out today.