Common Issues with Cold Water Booster Systems and How to Fix Them
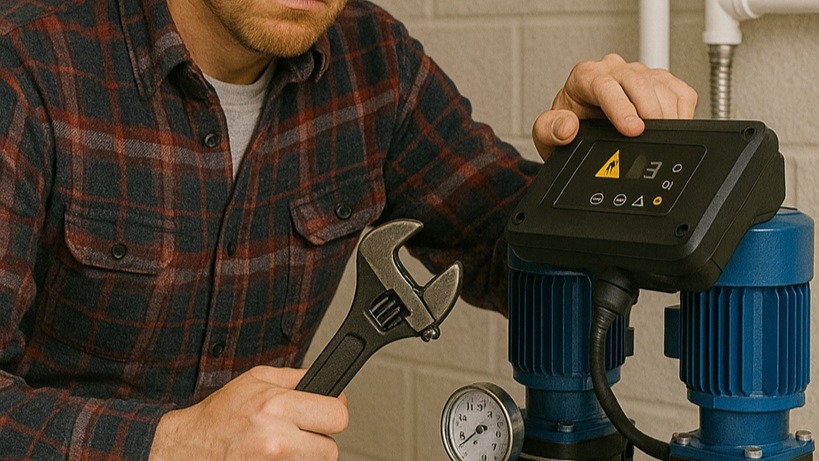
Cold water booster systems are the workhorses, ensuring adequate water pressure reaches every part of a busy commercial building. From hotels and offices to factories and hospitals, their reliable operation is crucial. Modern systems, like those supplied by National Pumps and Boilers, are designed for durability and efficiency. However, like any complex electromechanical system operating continuously, they can occasionally experience issues due to component wear, lack of maintenance, incorrect settings, or external factors. Recognising the common signs of trouble and understanding the potential causes is the first step towards effective resolution, minimising disruption and preventing minor faults from escalating into major failures. This guide explores common water pump pressure problems and other issues encountered with booster systems, offering insights into water pressure booster pump troubleshooting and guidance on when to call in the experts.
Understanding the System: A Foundation for Troubleshooting
Before diagnosing problems, it's helpful to recall the key interacting components typically found in packaged Pressurisation Units or booster sets:
- Pumps: Usually, one or more multi-stage centrifugal pumps provide the pressure increase.
- Motors: Drive the pumps (often controlled by VSDS in modern systems).
- Pressure Vessel(s): Air-charged tanks (Expansion Vessels) to buffer pressure and reduce pump cycling.
- Control Panel: Contains starters/VSDS, protection devices (overloads, dry run), control logic, sensors (pressure transducers), and user interface/alarms.
- Manifolds & Pipework: Connects pumps, vessels, and the system inlet/outlet.
- Valves: Isolation valves, check valves (Pump Valves), pressure relief valves.
- Sensors: Pressure transducers, level switches (for break tanks or dry run protection).
Problems often arise from the failure or incorrect setup of one or more of these interacting parts.
Common Issues with Cold Water Booster Systems: Symptoms & Potential Causes
Let's break down some frequent issues encountered by facilities managers and maintenance teams:
Issue 1: Consistently Low Water Pressure
- Symptoms: Weak flow from taps and showers throughout the building, or specifically on upper floors. Appliances like dishwashers or industrial processes may not function correctly. Readings on pressure gauges are consistently below the expected level. This is a classic sign of water pump pressure problems.
- Potential Causes (A Systematic Checklist):
- Inadequate Incoming Supply: Is the mains pressure itself unusually low? Is the break tank (if fitted) empty or slow to refill due to a faulty inlet valve or restricted mains supply? Is the main inlet strainer to the booster set blocked?
- Pump Performance Issue: Has one or more pumps failed (motor or wet end)? Are the impellers significantly worn, reducing efficiency and pressure output? Is the pump speed incorrectly set (too low) on a VSD system? Was the pump incorrectly sized for the building's actual demand during design/installation?
- System Blockages (Downstream): Are main filters or strainers within the building's distribution pipework clogged? Is a main isolation valve partially closed somewhere? Could a significant scale build-up in older pipework be restricting flow?
- Major Undetected Leak: Is there a significant leak somewhere in the building's distribution pipework, consuming a large volume of water and causing a pressure drop?
- Control System Fault: Is the pressure sensor providing an inaccurate (falsely high) reading to the controller? Is the VSD pressure setpoint programmed too low? Is the system incorrectly configured (e.g., only one pump running when more are needed)?
- Bypass Valve Open: Is a maintenance bypass valve accidentally left open, allowing water to circumvent the pumps?
- Initial Checks (Non-Specialist): Check break tank water level (if applicable). Verify main inlet valves to the set are fully open. Check accessible strainers. Observe the control panel for any fault indicators or status messages. Check pressure gauge readings. Note if all pumps are running during high-demand periods.
Issue 2: Fluctuating or Unstable Water Pressure
- Symptoms: Pressure noticeably surging high then dropping low, rapid on/off cycling of pumps (especially fixed speed), VSD systems 'hunting' (speed constantly ramping up and down). Can cause water hammer or inconsistent appliance operation.
- Potential Causes:
- Pressure Vessel Fault (Highly Common): This is the prime suspect for cycling/fluctuation issues.
- Incorrect Pre-charge: Air pressure in the vessel is too low (vessel becomes waterlogged, losing its buffering capacity) or too high (reduces usable water volume). Requires checking and adjusting with the system depressurised.
- Failed Diaphragm/Bladder: The Membrane inside the vessel has ruptured, allowing air to dissolve into the water or water to fill the air side. The vessel needs replacement.
- Undersized Vessel: The Vessel may be too small for the system volume or pump characteristics, leading to rapid pressure changes.
- Control System Settings:
- Fixed Speed: Pressure switch differential (gap between cut-in and cut-out pressure) set too narrow.
- Variable Speed: Poorly tuned PID control loop parameters causing instability or 'hunting'. The faulty pressure sensor is giving erratic readings.
- System Issues: Air trapped in the pipework or pumps. A faulty or slamming check valve is causing pressure surges. Rapidly opening/closing solenoid valves elsewhere in the system induce fluctuations.
- Pressure Vessel Fault (Highly Common): This is the prime suspect for cycling/fluctuation issues.
- Initial Checks: Observe pump cycling frequency. Check vessel condition visually (any external corrosion/damage?). Carefully check the vessel pre-charge only if competent and able to safely depressurise the system first – otherwise, this requires a professional. Observe control panel pressure readings for stability.
Issue 3: Excessively Noisy Operation
- Symptoms: Grinding, rattling, excessive humming, whining, banging noises emanating from the booster set or associated pipework.
- Potential Causes:
- Cavitation: Often a rumbling or gravelly sound. Caused by insufficient suction pressure (low tank level, blocked suction strainer/pipework, suction lift too high). Vapour bubbles form and collapse violently inside the pump, causing noise and severe damage over time.
- Air Entrainment: Gurgling or spitting noises. Air is being drawn into the system through leaks on the suction side or from a vortex in the break tank if the water level is too low.
- Mechanical Problems: Worn motor or pump bearings (consistent grinding or whining). Loose components (motor fan cover, panel doors, baseplate bolts) are causing rattling. A foreign object or debris inside the pump casing hits the impeller.
- Hydraulic Noise: Water hammer (loud banging) caused by sudden valve closures or pump stops/starts reacting against the long water column in risers. High water velocity in undersized pipes (general 'whooshing'). Resonance amplifies normal operational noise.
- Initial Checks: Verify the rear tank water level is adequate. Check suction valves are fully open and strainers clear. Listen carefully to pinpoint the source of the noise (motor end, pump wet end, specific valve, pipe section). Check baseplate bolts and covers for tightness.
Issue 4: System Fails to Start / No Water Delivery
- Symptoms: No water pressure build-up when demand occurs. Pumps do not run, or run briefly and trip out.
- Potential Causes:
- Electrical Supply Problems: No power to the control panel (check upstream breakers/fuses/isolators)? Emergency stop button pressed? Main control panel isolator switched off? Internal panel fuses blown? Temporary power outage?
- Control System Lockout/Fault: Control panel showing a fault condition (e.g., overload, dry run, phase failure)? System manually switched off at the panel? A 'remote stop' signal active (e.g., from BMS)? Faulty pressure sensor failing to detect low pressure and signal a start?
- Dry Run Protection Activated: Water level in break tank too low, activating level switch/probes? System detecting no-load condition on the motor?
- Pump/Motor Seizure: Complete mechanical failure preventing the pump/motor from turning (less common, usually preceded by noise/performance issues).
- Initial Checks: Check power supply indicators on the panel and upstream breakers. Check that E-stop buttons are released. Check the control panel display for status messages or fault codes. Check the break tank water level visually and/or the level indicators on the panel. Ensure panel selector switches are in 'Auto' mode. Do not attempt internal electrical checks unless fully qualified and authorised.
Issue 5: Water Leakage
- Symptoms: Puddles or drips around the booster set, visible water spray, wet patches on components, unexplained high water meter readings.
- Potential Causes:
- Pipe Connections: Loose flanges, unions, or threaded fittings. Failed gaskets or sealing compounds.
- Pump Mechanical Seal Failure: Leakage from where the motor shaft enters the pump casing. A common wear item, especially with age or poor water quality.
- Valve Failure: Leaking valve stem packing (around the handle) or failed body seals/gaskets.
- Pressure Vessel Issues: Leakage from pipe connection, air charging valve (Schrader valve), or potentially corrosion/failure of the vessel shell itself (serious).
- Component Cracks: Physical damage or stress fractures in pump casings, manifolds, or valve bodies.
- Initial Checks: Carefully identify the exact source of the leak. Note its severity (drip, seep, spray). Check the tightness of accessible fittings (without over-tightening). Isolate the leaking section using valves if possible and safe to do so, pending repair.
Effective Water Pressure Booster Pump Troubleshooting Steps
Approaching problems systematically is key. Here’s a structured approach to initial water pressure booster pump troubleshooting:
- Safety First: ALWAYS prioritise safety. Isolate electrical power using designated isolators before touching any components or removing covers. Be aware of potentially hot surfaces or pressurised water release when operating valves or checking components. If in any doubt, stop and call a professional.
- Observe & Gather Information: Note the exact symptoms. When did the problem start? Is it constant or intermittent? Are there any visual clues (leaks, damage)? What does the control panel indicate (status lights, fault messages, readings)? Are alarms sounding?
- Check the Basics:
- Power: Is power definitely available to the unit? Check indicators and upstream breakers.
- Water Supply: Is the inlet valve open? Is the break tank full? Is the inlet strainer clear?
- Control Settings: Is the system switched on and in 'Auto' mode? Are setpoints correct? Any active fault codes?
- Consult Documentation: Refer to the booster set's operating and maintenance manual. It often contains specific troubleshooting charts for common fault codes or symptoms. Check the commissioning report for initial settings.
- Systematic Diagnosis (Based on Symptoms - Refer to 'Potential Causes' above):
- Low Pressure: Start at the source (inlet) and work towards the discharge. Check supply -> check pump operation -> check downstream valves/filters.
- Fluctuations: Focus on the pressure vessel (pre-charge!) and control system settings/sensors.
- Noise: Try to pinpoint the source accurately. Check suction conditions first for cavitation/air.
- Failure to Start: Check the power path and control system permissive/fault signals methodically.
- Leaks: Identify the precise location.
- Know Your Limits: Perform only basic visual checks and simple actions (like checking valve positions or clearing easily accessible strainers) unless you are fully trained and competent in booster system maintenance. Avoid attempting complex repairs, internal electrical work, or adjustments to critical control parameters without proper expertise.
Preventative Maintenance: Avoiding Problems in the First Place
The most effective way to deal with water pump pressure problems and other issues is to prevent them. Regular, planned preventative maintenance is crucial:
- Routine Inspections (e.g., Weekly/Monthly by site staff): Visual check for leaks, unusual noise/vibration. Check pressure gauge readings are normal. Check control panel status lights/display. Check break tank level. Keep the area around the set clean and accessible.
- Scheduled Checks (e.g., Quarterly/Semi-Annually by competent personnel): Clean accessible strainers. Exercise valves to prevent seizure. Verify basic control functions. More thorough visual inspection.
- Professional Servicing (e.g., Annually): This is essential and should include:
- Pressure Vessel Pre-charge Check & Adjustment: The single most important preventative check. Must be done correctly with the system depressurised.
- Pump Performance Check: Assessing pressure/flow delivery, checking motor current draw.
- Seal and Bearing Check: Listening for bearing noise, visual inspection for seal leaks.
- Valve Inspection & Test: Checking for leaks and correct operation (especially check valves and PRVS if fitted).
- Control Panel & Safety Device Testing: Verifying overload settings, testing dry run protection, checking sensor calibration, and testing alarms.
- Electrical Connection Check: Inspecting terminal tightness and wiring condition (qualified electrician).
- Record Keeping: Maintain a detailed logbook of all inspections, readings, maintenance actions, and any issues encountered. This history is invaluable for future troubleshooting.
National Pumps and Boilers offers tailored preventative maintenance contracts designed to keep your booster system reliable and efficient.
When to Call the Professionals
While basic awareness helps, many booster system issues require expert diagnosis and repair. Call a qualified engineer, like the team at National Pumps and Boilers, when:
- You suspect any electrical faults or issues within the control panel.
- There are major or persistent leaks.
- The system frequently trips on overload, dry run, or other protections.
- Low pressure or fluctuation problems persist after basic checks (especially if vessel pre-charge is suspected).
- Unusual noises (grinding, severe vibration) indicate potential internal pump/motor damage.
- You lack the necessary tools, expertise, or competence to safely diagnose or repair the issue.
- Pressure vessel testing or re-certification is required.
- Any work requires a significant component of disassembly or replacement.
Attempting complex repairs without proper knowledge can lead to further damage, safety risks, and voided warranties.
Why Choose National Pumps and Boilers for Troubleshooting and Maintenance?
Dealing with water pump pressure problems requires specialist knowledge. At National Pumps and Boilers, we provide:
- Expert Diagnostics: Our experienced engineers are skilled in water pressure booster pump troubleshooting, quickly identifying root causes using systematic methods and diagnostic tools.
- Qualified Repairs: We carry out repairs using genuine spare parts for major Brands, ensuring quality and compatibility.
- Preventative Maintenance Contracts: Tailored plans to suit your system and budget, minimising unexpected breakdowns and optimising performance.
- System Optimisation: We can advise on upgrades or adjustments to improve efficiency and reliability based on performance data and site conditions.
Keep Your Water Flowing Smoothly
Cold water booster systems are vital assets for commercial buildings. Understanding common issues and the basics of troubleshooting empowers facilities staff to perform initial checks and provide accurate information when seeking professional help. However, prioritising regular preventative maintenance and relying on expert engineers for complex diagnostics and repairs is the key to long-term reliability and avoiding disruptive water pump pressure problems.
If you're experiencing issues with your cold water booster system, require expert water pressure booster pump troubleshooting, or want to set up a preventative maintenance plan, Contact National Pumps and Boilers today. We're here to ensure your building's water supply remains consistently strong and reliable.