Common Issues with Submersible Pumps and How to Troubleshoot Them
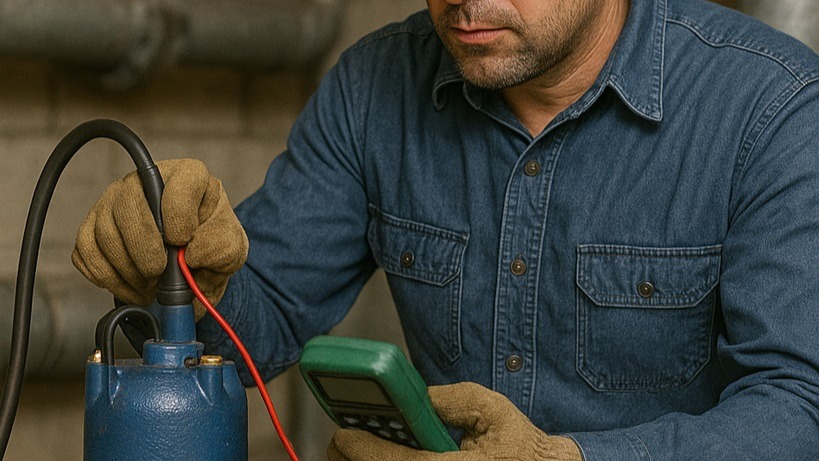
Submersible pumps are the unsung heroes of water management across countless applications in the UK. From ensuring a clean water supply in domestic boreholes and managing construction site dewatering to handling critical processes in industrial settings and wastewater treatment plants, these powerful machines operate reliably beneath the surface. However, like any hard-working piece of equipment, they aren't immune to issues. Encountering submersible pump problems can disrupt operations, lead to costly downtime, and cause significant frustration.
Fortunately, understanding the common culprits behind pump failures and knowing basic troubleshooting steps can empower you to address minor issues quickly. For more complex situations, knowing when to call in professionals for expert submersible water pump repair is crucial. At National Pumps and Boilers, we specialise in keeping these vital systems running smoothly. This comprehensive guide will delve into the typical challenges faced by submersible pump users and provide practical advice on diagnosis and resolution.
Getting to Grips with Submersible Pumps: More Than Just a Motor Underwater
Before diving into the problems, let's solidify our understanding of these essential devices. A submersible pump, by definition, is designed to be fully submerged within the fluid it needs to move. Its defining feature is a hermetically sealed motor close-coupled to the pump body. This design offers several advantages:
- Self-Priming: Being submerged eliminates the need for priming, unlike many surface-level pumps.
- Efficiency: Pushing fluid is generally more energy-efficient than pulling it (suction lift). The surrounding water also helps cool the motor.
- Space Saving: Ideal for installations where space is limited, such as narrow wells or sumps.
- Quiet Operation: Submersion significantly dampens operational noise.
How They Work: The Science Below the Surface
Most submersible pumps operate on the principle of centrifugal force. Here’s a simplified breakdown:
- Motor Power: An electric motor, sealed against water ingress, provides the rotational energy.
- Impeller Rotation: The motor shaft spins one or more impellers housed within the pump casing (volute).
- Fluid Acceleration: As the impeller(s) rotate at high speed, they impart kinetic energy to the surrounding fluid, forcing it outwards by centrifugal force.
- Pressure Conversion: The shape of the pump casing (volute) is designed to slow down the fluid flow, converting the kinetic energy into pressure energy.
- Discharge: This increased pressure forces the fluid up through the discharge pipe to the surface or its intended destination.
Key Components You Should Know
Understanding the anatomy of your submersible pump can greatly assist in diagnosing issues:
- Motor: The powerhouse of the pump. Can be oil-filled or water-filled for cooling and lubrication. Requires robust sealing.
- Impeller: The rotating component with vanes that transfers energy to the fluid. Different designs exist (open, semi-open, vortex, closed) depending on the application (clean water, sewage, solids handling). Materials vary from engineered plastics to bronze and stainless steel.
- Seals: Critical for preventing water from entering the motor housing. Mechanical seals are common, often consisting of hard-faced rings (like silicon carbide or tungsten carbide) pressed together. Lip seals may also be used. Seal failure is a frequent cause of submersible pump problems.
- Pump Casing (Volute): Surrounds the impeller and directs the flow towards the discharge outlet.
- Intake Screen: Prevents large debris from entering the pump, though finer particles can still pass through.
- Power Cable: Specially designed waterproof cable to deliver electricity safely to the submerged motor. Cable damage can lead to serious electrical faults.
- Bearings: Support the motor shaft, ensuring smooth rotation. Wear or failure can cause noise, vibration, and eventual seizure.
- Control Panel (Often Surface Level): Houses starters, capacitors (for single-phase motors), overload protection, and control logic (like float switches or pressure switches).
Types of Submersible Pumps and Their Applications
Submersible pumps are not a one-size-fits-all solution. Different designs cater to specific needs:
- Borehole/Well Pumps: Long, slender pumps designed to fit inside deep wells for extracting groundwater. Brands like Grundfos, Lowara, and Ebara offer robust solutions in this category.
- Sump Pumps: Used in basements and crawl spaces to remove accumulated water and prevent flooding. Often automatically controlled by a float switch.
- Sewage Pumps: Designed to handle wastewater containing soft solids. Often feature vortex or grinder impellers. Wilo and Dab are prominent names here.
- Effluent Pumps: Handle 'greywater' with smaller suspended solids, typically from septic systems.
- Grinder Pumps: Feature cutting mechanisms to macerate sewage solids into a fine slurry, allowing it to be pumped through smaller diameter pipes over longer distances.
- Dewatering Pumps: Rugged pumps used on construction sites and in mines to remove large volumes of water, often containing abrasive particles.
National Pumps and Boilers offers a wide selection across these types – browse our Submersible Pumps category to explore options.
Diagnosing and Troubleshooting Common Submersible Pump Problems
Even the most reliable pumps from top manufacturers can experience issues over their lifespan. Being able to identify the symptoms and understand the potential causes is the first step towards resolution. Here’s a deeper look into the most frequent submersible pump problems:
Problem 1: The Pump Refuses to Start
Pressing the 'on' switch or expecting automatic activation, only to be met with silence, is a common and frustrating scenario.
Symptoms:
- Complete lack of operation when power is supplied.
- No sound (humming, clicking) from the pump or control panel.
Potential Causes & Detailed Troubleshooting:
- Power Supply Issues:
- Tripped Circuit Breaker/Blown Fuse: This is the first place to check. Has a breaker in your main electrical panel or the dedicated pump control box tripped? Reset it ONCE. If it trips again immediately, there's likely a short circuit or severe overload requiring investigation – do not keep resetting it. Ensure the breaker is correctly sized for the pump's load.
- No Power to the Control Panel: Use a multimeter (exercising extreme caution) to verify voltage is reaching the control panel terminals. Check isolator switches.
- Faulty Wiring/Connections: Look for loose wires, corroded terminals, or damaged insulation within the control box, junction boxes, and at the pump connection (if accessible). Water ingress into electrical enclosures is a common culprit.
- Incorrect Voltage/Phase: Verify the supplied voltage matches the pump's nameplate rating. For 3-phase pumps, check that all three phases are present and balanced.
- Control System Faults:
- Faulty Float Switch/Pressure Switch: If the pump is controlled automatically, the switch might be stuck open or faulty, preventing activation. Manually test the switch if possible or bypass it temporarily (for testing only by qualified personnel) to see if the pump runs.
- Defective Contactor/Relay: In the control panel, the contactor or relay that switches the power to the pump might have failed (burnt contacts, coil failure). Listen for a 'click' when the pump should start.
- Capacitor Failure (Single-Phase Pumps): Single-phase motors often use start and/or run capacitors. A faulty capacitor can prevent the motor from starting or running correctly. Look for bulging or leaking capacitors.
- Motor Issues:
- Seized Motor/Pump: The motor bearings might have seized, or the pump end might be jammed with debris, preventing rotation. This usually causes an overload trip.
- Burnt Motor Windings: A catastrophic failure often caused by prolonged overheating, voltage problems, or seal failure leading to water ingress. This typically results in an immediate trip or no response. Requires professional submersible water pump repair or replacement.
Troubleshooting Approach: Start systematically. Check power at the source, then the control panel, then the wiring. Listen for sounds. If basic checks don't reveal the issue, or if breakers trip repeatedly, it's time to suspect a more serious fault within the pump or motor itself. Electrical troubleshooting can be dangerous; if unsure, contact professionals like National Pumps and Boilers.
Problem 2: Reduced Flow Rate or No Water Delivery
Your pump is running, but the amount of water reaching the destination is significantly less than expected, or perhaps none at all.
Symptoms:
- Noticeably lower water pressure or volume at outlets.
- The pump runs continuously without satisfying the demand.
- No water delivery despite the pump motor running.
Potential Causes & Detailed Troubleshooting:
- Blockages:
- Clogged Intake Screen: Sediment, leaves, plastic bags, or bio-fouling can restrict water entry. Requires lifting the pump (if possible) for cleaning.
- Blocked Impeller: Debris passing the screen can jam the impeller. Symptoms might include noise and reduced flow. Requires dismantling the pump end for cleaning – a task often best left for submersible water pump repair specialists.
- Obstructed Discharge Line: Check for partially closed valves (Pump Valves category), kinks in flexible hoses, or sediment build-up inside pipes, especially on long runs or bends. Flushing the line might help.
- Pump Wear and Tear:
- Worn Impeller/Volute: Abrasive particles (sand, grit) gradually erode the impeller vanes and casing, reducing efficiency. Flow and pressure will decrease over time. Requires replacement of worn parts.
- Worn Wear Rings: Some pumps have replaceable wear rings to maintain close tolerances. As these wear, internal recirculation increases, reducing output.
- System Issues:
- Airlock: Air trapped in the pump or discharge line can prevent water from being pumped effectively. Requires bleeding procedures, which vary by installation.
- Low Water Level (Source Depletion): Is the water level in the well, sump, or tank simply too low for the pump intake? The pump might be sucking air.
- Incorrect Pump Selection/Sizing: Was the pump correctly matched to the system's requirements (Total Dynamic Head and flow)? If system conditions have changed (e.g., higher lift required), the pump may no longer be adequate. Consult our team via the Homepage for help with pump selection.
- Leaks in the Discharge Line: Water escaping through cracks or bad joints before the outlet will reduce the delivered flow.
- Motor Issues (Less Common for Flow Reduction Alone):
- Motor Running Backwards (3-Phase): If phases are connected incorrectly, the motor spins the wrong way, resulting in very low flow/pressure. Swap any two phases (requires a qualified electrician).
Troubleshooting Approach: Start with the easiest checks: water level, valve positions, visible obstructions. Check pump running amps – higher than normal might indicate a blockage, lower than normal could suggest running dry or severe wear. Inspecting internal components often requires pump removal and professional service.
Problem 3: Pump Overheating
An excessively hot pump motor is a serious warning sign that requires immediate attention to prevent permanent damage.
Symptoms:
- Pump casing feels unusually hot to the touch (exercise caution).
- Thermal overload protection trips frequently.
- Smell of burning insulation.
- Steam emanating from the pump area (if partially submerged).
Potential Causes & Detailed Troubleshooting:
- Running Dry/Insufficient Submergence: The most common cause. Submersible pumps rely on the surrounding fluid for cooling. If the water level drops below the motor housing (or minimum required level specified by the manufacturer), it cannot dissipate heat effectively. Ensure adequate water level. Check float switch settings.
- Blocked Intake/Discharge: A severe blockage makes the pump work much harder, generating excess heat. Refer to troubleshooting for Problem 2.
- Operating Off-Curve: Forcing the pump to operate far outside its Best Efficiency Point (BEP) – either too high flow (low head) or too low flow (high head) – can cause inefficiency and motor heating. This relates to proper pump selection and system design.
- Incorrect Voltage: Consistently high or low voltage stresses the motor windings, generating extra heat. Verify power supply quality.
- Internal Mechanical Friction: Worn bearings or an impeller rubbing against the casing generate heat through friction. Often accompanied by noise (see Problem 4).
- Blocked Motor Cooling Passages: Some larger submersibles have internal or external cooling jackets. If these become blocked by sediment or scale, cooling efficiency is reduced.
- High Ambient Fluid Temperature: If the fluid being pumped is already very hot, the motor's ability to cool itself is diminished. Ensure the pump is rated for the fluid temperature.
Troubleshooting Approach: Immediately check the water level and ensure proper submergence. Check for obvious blockages. Monitor pump temperature if safe to do so. If the pump frequently trips on thermal overload, investigate the cause thoroughly – repeated overheating drastically shortens motor life and leads to expensive submersible water pump repair or replacement.
Problem 4: Unusual Noises or Vibration
A submersible pump in good condition should operate relatively quietly. Grinding, rattling, or excessive vibration indicates a problem.
Symptoms:
- Grinding, scraping sounds.
- Rattling or clunking noises.
- Excessive vibration is felt on the discharge pipe or mounting.
- Loud humming or buzzing.
- Gurgling or popping sounds (cavitation).
Potential Causes & Detailed Troubleshooting:
- Debris in Pump: Stones, gravel, or other solids hitting the impeller or rattling inside the casing. Requires stopping the pump and attempting to clear the blockage (potentially requiring disassembly).
- Worn Bearings: A common cause of grinding or screeching noises. Noise may worsen under load. Requires bearing replacement – a job for a submersible water pump repair workshop.
- Damaged/Loose Impeller: An impeller with broken vanes or one that has become loose on the shaft will cause noise and imbalance (vibration).
- Cavitation: Occurs when the pressure at the pump inlet drops below the vapour pressure of the fluid, causing vapour bubbles to form and collapse violently. Sounds like pumping gravel. Causes include blocked suction, excessive lift, or pumping overly hot liquids. Addressing cavitation is crucial as it rapidly damages impellers and casings. Check intake conditions and ensure the pump is suitable for the application.
- Electrical Humming/Buzzing: Can indicate an electrical fault, such as a failing capacitor or issues with the motor windings or power supply. Investigate electrical components.
- Pump Touching Sides of Sump/Well: Vibration can be amplified if the pump body is knocking against the walls of its enclosure. Ensure proper installation and clearance.
Troubleshooting Approach: Try to characterise the noise. Is it constant or intermittent? Does it change with load? Check for vibration. Noise is often an early indicator of wear or damage; investigating promptly can prevent catastrophic failure. Addressing underlying submersible pump problems causing noise is key.
Problem 5: Water Leaking From or Around the Pump
While the pump itself is submerged, leaks can occur at connections or due to component failure, sometimes noticeable if the pump is lifted or if leaks occur in discharge piping above water level. More critically, internal leaks compromise the motor.
Symptoms:
- Visible water leaks from casing joints, seals, or discharge connections when the pump is lifted for inspection.
- Oil slick on water surface (indicates motor seal failure in oil-filled motors).
- Water was detected inside the motor housing during service (major seal failure).
- Reduced performance accompanied by signs of leakage.
Potential Causes & Detailed Troubleshooting:
- Seal Failure: This is the most critical leak type. Mechanical seals wear over time, especially with abrasive fluids or dry running. Damage allows water into the motor housing (water-filled motor) or oil out/water in (oil-filled motor), leading to rapid motor failure. Seal replacement is a standard submersible water pump repair procedure, but it requires expertise.
- Damaged Gaskets/O-Rings: Seals between pump casing sections or cable entry glands can degrade or be damaged, allowing leaks. Requires replacement.
- Cracked Casing: Physical impact or freezing can crack the pump housing. Often requires pump replacement.
- Loose Fittings/Connections: Discharge pipe connections might loosen due to vibration. Check and tighten threaded or flanged joints. Ensure appropriate sealants or gaskets are used.
Troubleshooting Approach: Inspect the pump visually for leak sources when accessible. Oil presence is a strong indicator of main seal failure. Any sign of water ingress into the motor necessitates immediate professional attention to prevent burnout. Contact National Pumps and Boilers for seal diagnostics and replacement.
Problem 6: Pump Cycling On and Off Too Frequently (Short Cycling)
The pump turns on, runs for a very short period, turns off, and then quickly repeats the cycle. This puts excessive wear on the motor and controls, and consumes more energy.
Symptoms:
- Pump runs for seconds rather than minutes.
- Rapid clicking sounds from the pressure switch or control panel.
- Fluctuating water pressure.
Potential Causes & Detailed Troubleshooting:
- Waterlogged Pressure Tank / Expansion Vessel: The most common cause in pressure-boosted systems. The tank (Expansion Vessels category) loses its air cushion, meaning the slightest drop in pressure (e.g., opening a tap briefly) causes the pump to start, and minimal pumping brings it back to cut-off pressure immediately. Check and recharge the air pressure in the tank (when the pump is off and system depressurised) according to manufacturer instructions (e.g., for brands like Reflex or Flamco). If it won't hold air, the bladder/diaphragm may have failed, requiring tank replacement.
- Faulty/Incorrectly Set Pressure Switch: The device telling the pump when to start and stop might be defective or have its cut-in/cut-out pressures set too close together. Inspect, adjust (carefully), or replace the pressure switch.
- Faulty Check Valve / Non-Return Valve: A check valve (Pump Valves category) prevents water from flowing back down into the well/sump when the pump stops. If it fails, pressure drops rapidly, causing the pump to restart. Listen for water flowing back; inspect/replace the valve.
- Leaks in the Plumbing System: Even a small leak downstream of the pump will cause pressure to drop gradually, triggering the pump. Check taps, toilets, and pipework for hidden leaks.
- Pump Oversized for Tank/Demand: If the pump delivers water much faster than the pressure tank can handle or the demand requires, it will reach the cut-off pressure very quickly.
Troubleshooting Approach: Start with the pressure tank air charge. Then, investigate the pressure switch and check valve. Finally, check thoroughly for system leaks. Short cycling significantly shortens the life of your pump and related components.
Advanced Troubleshooting Tools and Techniques
While basic observation goes a long way, sometimes more sophisticated tools are needed for accurate diagnosis:
- Multimeter: Essential for checking voltage, continuity, and resistance in electrical circuits (control panels, wiring, motor windings).
- Megohmmeter (Megger): Used to test motor winding insulation resistance. Low readings indicate insulation breakdown, often due to overheating or moisture ingress – a key test in professional submersible water pump repair.
- Clamp Meter: Measures the current (Amps) drawn by the motor without disconnecting wires. Comparing readings to the nameplate rating helps diagnose overload, underload (running dry), or winding faults.
- Pressure Gauge: Measuring discharge pressure is vital for diagnosing flow issues and checking pressure switch operation.
- Flow Meter: Accurately measures the actual flow rate being delivered, useful for diagnosing performance issues and comparing against the pump curve.
Understanding pump curves (provided by manufacturers like Grundfos, Lowara, etc.) and how they relate to your system curve (resistance from pipes, valves, elevation) is crucial for advanced troubleshooting and ensuring correct pump selection initially.
The Power of Preventive Maintenance: Avoiding Problems Before They Start
The most cost-effective approach to managing submersible pump problems is prevention. A regular maintenance schedule can catch minor issues before they escalate into major failures requiring extensive submersible water pump repair.
Key Preventative Maintenance Tasks:
- Regular Visual Inspections:
- Check for leaks around any visible pipework and connections.
- Listen for unusual noises or vibrations during operation.
- Inspect the control panel for signs of overheating, loose connections, or moisture.
- Check the condition of the power cable for any damage or wear, especially near the pump entry point.
- Monitor pump cycling frequency (if applicable).
- Performance Monitoring:
- Periodically check flow rate and pressure (if gauges are installed) to spot gradual declines.
- Monitor energy consumption – a sudden increase can indicate inefficiency or a developing problem.
- Record operating parameters (amps, voltage, pressure) to establish a baseline for comparison.
- Scheduled Cleaning:
- Depending on the application and water quality, periodically lift the pump (if feasible) to clean the intake screen. Sump pumps and sewage pumps may require more frequent checks for debris.
- Electrical System Checks:
- Ensure all electrical connections in the control panel are tight and corrosion-free.
- Test overload protection devices periodically.
- Consider periodic megger testing of the motor insulation, especially for critical applications.
- Seal & Bearing Checks (Professional Service):
- During major services, seals and bearings should be inspected for wear and replaced proactively based on operating hours or condition, rather than waiting for failure.
- Water Quality Awareness:
- Understand the quality of the water being pumped. Abrasive sand or corrosive water will accelerate wear on impellers and seals. Water analysis can inform material selection and maintenance frequency.
- Pressure Tank Maintenance (If Applicable):
- Regularly check and maintain the air charge in expansion vessels as described under 'Short Cycling'.
Implementing a preventative maintenance plan, potentially through a service agreement with specialists like National Pumps and Boilers, offers peace of mind and maximises the lifespan and reliability of your submersible pump system.
When DIY Isn't Enough: Calling in the Professionals
While basic troubleshooting can resolve some issues, many submersible pump problems require specialised knowledge, tools, and safety precautions. It's time to call for professional submersible water pump repair when:
- Electrical Faults Persist: Repeatedly tripping breakers, suspected motor winding issues, or complex control panel faults require a qualified electrician or pump technician. Working with pump electrics, especially in wet environments, is dangerous.
- Internal Pump/Motor Issues Suspected: Grinding noises, confirmed seal failure (oil leak/water in motor), severely damaged impeller, or seized motor necessitate pump removal and workshop repair.
- Pump Requires Lifting/Disassembly: Many submersible pump repairs require pulling the pump from its well or sump, which can be difficult and requires proper equipment. Disassembly and reassembly, especially replacing seals, require expertise.
- Problem Persists After Basic Troubleshooting: If you've checked the common causes and the issue remains unresolved, an expert diagnosis can save time and prevent further damage.
- Safety Concerns: If you feel unsure or unsafe performing any checks or repairs, always defer to a professional.
Benefits of Using National Pumps and Boilers:
- Expert Diagnosis: Our experienced technicians can quickly pinpoint the root cause of complex submersible pump problems.
- Specialised Tools: We have the necessary equipment for lifting pumps, testing motors (including megger testing), and performing intricate repairs.
- Genuine Parts: We use high-quality replacement parts, including components for major brands like Wilo, Grundfos, Lowara, DAB, Ebara, and Stuart Turner.
- Efficient Repairs: We aim to get your system back online quickly, minimising downtime.
- Safety Compliant: All work is carried out safely and according to relevant regulations.
- Comprehensive Services: Beyond repair, we offer preventative maintenance plans, new pump supply and installation, and system advice. Explore our full range of services on our Homepage.
Choosing the Right Pump: Prevention Starts at Selection
Many downstream submersible pump problems originate from selecting a pump that isn't quite right for the job. Factors to consider include:
- Application: Is it for clean water, wastewater, or drainage? This dictates the pump type (borehole, sewage, sump, etc.).
- Flow Rate: How much fluid needs to be moved per minute or hour?
- Total Dynamic Head (TDH): The total resistance the pump must overcome, including vertical lift and friction losses in the pipework. Undersizing leads to poor performance; oversizing can cause inefficiency, short cycling, and wear.
- Fluid Characteristics: Temperature, viscosity, presence of solids (size and concentration), chemical composition. This affects material choice and impeller type.
- Electrical Supply: Available voltage and phase (single or three-phase).
- Installation Constraints: Borehole diameter, sump size.
Consulting with pump specialists like the team at National Pumps and Boilers during the selection process ensures you get a pump correctly sized and specified for your needs, providing reliable and efficient operation for years to come.
Keep Your Water Moving: Partner with National Pumps and Boilers
Submersible pumps are critical assets. Understanding potential submersible pump problems, performing basic checks, and committing to preventative maintenance are key to their longevity. However, when complex issues arise or professional expertise is needed for diagnosis or submersible water pump repair, you need a reliable partner.
National Pumps and Boilers offers extensive experience across all types of submersible pumps and major brands. Whether you're facing an emergency breakdown, planning preventative maintenance, or considering a new installation, our team is ready to assist. We are committed to providing efficient, effective solutions to keep your water management systems performing optimally.
Don't let pump problems disrupt your operations. If you need assistance with troubleshooting, repair, or maintenance for your submersible pumps, contact National Pumps and Boilers today. Let us provide the expert support you need for reliable water management.