Common Problems with Pressurisation Units and How to Fix Them
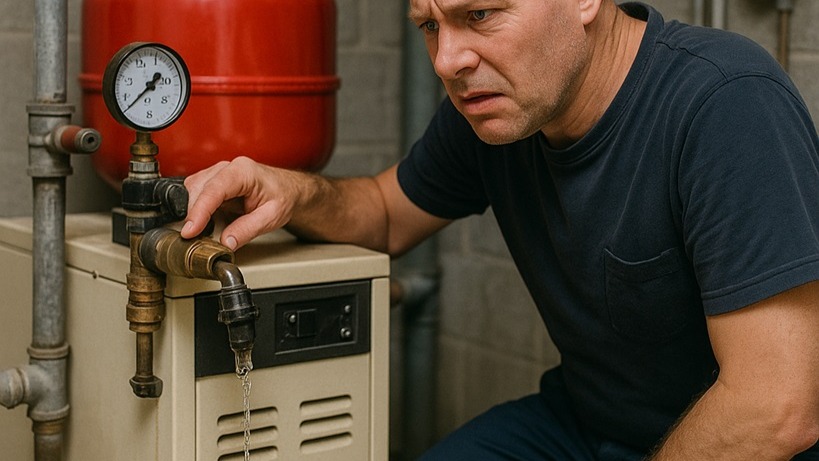
Pressurisation units stand as the silent guardians of commercial and industrial heating systems, playing an indispensable role in maintaining the delicate equilibrium of pressure required for optimal performance. These sophisticated devices ensure that heating systems operate efficiently, preventing a cascade of problems that can lead to discomfort, operational disruptions, and increased energy consumption. Recognising the early signs of pressurisation unit issues and understanding effective troubleshooting pressurisation units techniques are crucial for facility managers and maintenance personnel. This comprehensive guide will delve deeper into the common problems encountered with pressurisation units, providing detailed explanations of their causes, step-by-step solutions, and proactive maintenance strategies to ensure the longevity and reliability of your heating infrastructure.
A Deeper Look into the Role of Pressurisation Units
To truly appreciate the significance of addressing potential problems, it's vital to have a thorough understanding of the fundamental role that pressurisation units play within closed-loop heating systems. These systems, unlike open systems, recirculate the same water, which is heated and distributed throughout the building. The pressurisation unit's primary function is to compensate for volume changes in the water due to temperature fluctuations. As water heats up, it expands, and as it cools down, it contracts. Without a pressurisation unit, this expansion and contraction would lead to significant pressure variations, potentially causing damage to system components such as pipes, boilers, and radiators.
Furthermore, pressurisation units maintain a positive pressure within the system, preventing the ingress of air. Air in the system can lead to corrosion, noisy operation, and reduced heat transfer efficiency. Modern pressurisation units often incorporate sophisticated controls and sensors to monitor pressure in real-time and automatically adjust it by either releasing excess pressure or adding water as needed. Understanding this intricate balancing act underscores the importance of addressing any pressurisation unit issues promptly to safeguard the entire heating infrastructure. For comprehensive solutions related to maintaining the heart of your heating system, explore our offerings in Central Heating.
Comprehensive Analysis of Common Pressurisation Unit Issues and Advanced Troubleshooting Techniques
Let's delve into a more detailed examination of the common problems that can plague pressurisation units, along with advanced troubleshooting pressurisation units methodologies and in-depth repair strategies.
1. Persistent Fluctuating Pressure Levels: Beyond the Basics
While simple recalibration and bleeding can often resolve minor pressure fluctuations, persistent instability indicates a more complex underlying issue.
- Advanced Causes: Beyond faulty sensors and trapped air, fluctuating pressure can also be caused by a malfunctioning expansion vessel. The expansion vessel is designed to accommodate the changes in water volume. If its internal bladder is damaged or has lost its pre-charge, it will not effectively buffer pressure changes. Another potential cause could be a faulty pressure relief valve that is opening and closing prematurely.
- Advanced Troubleshooting and Fixes:
- Expansion Vessel Check: Isolate the expansion vessel and check its pre-charge pressure using a tyre pressure gauge. If the pressure is significantly different from the manufacturer's specification (typically around 1.5 bar when the system is cold), the vessel may need recharging or replacement. We offer a range of high-quality Expansion Vessels from trusted brands like Reflex and Flamco.
- Sensor Diagnostics: Use a multimeter to test the resistance of the pressure sensor. Compare the readings with the manufacturer's specifications to identify any inconsistencies. Faulty sensors will require replacement.
- System Bleeding Protocol: Ensure a thorough bleeding process by systematically venting air from all high points in the system, including radiators and air vents on pumps and other components.
- Calibration Verification: Double-check the calibration of the pressurisation unit's control panel against a calibrated pressure gauge to ensure accuracy.
2. Recurrent Boiler Shutdowns: Investigating Deeper
Frequent boiler shutdowns are a serious concern and require a systematic approach to identify the root cause.
- Advanced Causes: While low water pressure and pump failure are common culprits, other factors can contribute to this issue. A blocked or partially closed isolation valve in the system can restrict water flow and lead to low pressure at the boiler. Similarly, a faulty flow switch or pressure switch within the boiler itself might be incorrectly triggering shutdowns.
- Advanced Troubleshooting and Fixes:
- Systematic Pressure Testing: Use a calibrated pressure gauge at various points in the system to identify pressure drops that might indicate blockages or leaks.
- Pump Performance Analysis: Check the pump's electrical connections, motor windings, and impeller for any signs of damage or malfunction. Measure the pump's discharge pressure to assess its performance against the manufacturer's specifications. Explore our reliable pump options from leading manufacturers like Grundfos and Lowara.
- Valve Inspection: Carefully inspect all isolation valves in the heating system to ensure they are fully open and not obstructed.
- Boiler Control Diagnostics: If the system pressure is adequate, investigate the boiler's internal controls, such as flow switches and pressure switches, which might be malfunctioning. This often requires specialist knowledge.
3. Excessive Noisy Operation: Pinpointing the Source
Unusual noises can range from irritating to indicative of significant mechanical problems.
- Advanced Causes: Beyond cavitation and airlocks, worn-out pump bearings can produce grinding or whining noises. Vibrations caused by loose mountings or pipework can also amplify operational sounds. In some cases, the noise might originate from scale buildup within the heat exchanger or other system components, restricting flow and causing turbulence.
- Advanced Troubleshooting and Fixes:
- Cavitation Analysis: Ensure the system's net positive suction head (NPSH) requirements are being met. Restrictions on the suction side of the pump can lower pressure and lead to cavitation.
- Airlock Elimination Protocol: Implement a thorough air bleeding procedure, potentially requiring the use of automatic air vents at strategic locations.
- Pump Bearing Assessment: If a grinding or whining noise is present, the pump bearings may be failing and require replacement or pump overhaul. Consider our range of high-quality pumps from Wilo and DAB.
- Vibration Dampening: Inspect and tighten any loose pump mountings or pipe supports. Consider installing vibration isolators to reduce noise transmission.
- System Cleaning and Descaling: If scale buildup is suspected, a chemical cleaning or descaling of the system might be necessary.
4. Persistent Water Leaks: Locating and Addressing the Source
Even small leaks can lead to significant water loss, pressure drops, and potential damage over time.
- Advanced Causes: While loose connections and damaged seals are common, leaks can also occur due to corrosion of pipes or components, particularly at joints and welds. Stress cracks caused by thermal expansion and contraction over extended periods can also lead to leaks.
- Advanced Troubleshooting and Fixes:
- Systematic Leak Detection: Conduct a thorough visual inspection of all pipework, connections, valves, and the pressurisation unit itself. Look for signs of moisture, corrosion, or mineral deposits.
- Pressure Testing for Leaks: Isolate sections of the heating system and perform pressure tests to pinpoint the location of less obvious leaks.
- Professional Repair Techniques: Depending on the severity and location of the leak, repairs might involve tightening connections, replacing seals or gaskets, or welding or replacing corroded pipe sections. For complex repairs, it's best to consult professionals. We can connect you with experienced technicians – please Contact Us.
5. System Filling Impairment: Diagnosing the Restriction
When the pressurisation unit struggles to maintain the required pressure due to inadequate filling, it indicates a blockage or malfunction in the water supply system.
- Advanced Causes: Blocked non-return valves in the filling line, a closed or partially obstructed mains water supply valve, or a malfunctioning automatic filling valve within the pressurisation unit can all prevent proper filling. In some cases, a significant leak elsewhere in the system might exceed the filling capacity of the unit.
- Advanced Troubleshooting and Fixes:
- Filling Line Inspection: Trace the water supply line to the pressurisation unit and check for any closed or partially closed valves. Inspect non-return valves for blockages or malfunctions.
- Automatic Filling Valve Assessment: Test the operation of the automatic filling valve. It might be stuck closed or have a faulty actuator. Replacement of the valve might be necessary.
- Leakage Rate Analysis: If the filling system appears to be functioning correctly, investigate the possibility of a significant leak in the heating system that is preventing the pressure from building up.
Proactive Preventive Maintenance: Ensuring Long-Term Reliability
Implementing a comprehensive preventative maintenance program is the most effective way to minimise pressurisation unit issues and ensure the long-term reliability of your commercial heating system.
- Detailed Regular Inspections: Schedule regular inspections (e.g., monthly or quarterly) that go beyond a quick visual check. This should include checking pressure readings, listening for unusual noises, inspecting for leaks, and verifying the operation of all components.
- Comprehensive Cleaning and Descaling Procedures: Implement a schedule for cleaning filters, strainers, and pump components. Depending on the water hardness in your area, consider periodic descaling of the pressurisation unit and other system components to prevent scale buildup.
- Thorough Documentation and Performance Monitoring: Maintain detailed records of all maintenance activities, repairs, and pressure readings over time. This data can help identify trends, predict potential failures, and optimise maintenance schedules. Consider using building management systems (BMS) to monitor system performance and generate alerts for any deviations from normal operating parameters.
- Expansion Vessel Maintenance: Regularly check the pre-charge pressure of the expansion vessel (at least annually) and recharge it as necessary.
- Sensor Calibration and Testing: Periodically calibrate and test the pressure sensors to ensure accurate readings.
- Valve Exercising: Regularly exercise all valves in the system to prevent them from seizing.
When Professional Intervention is Essential: Recognising Limitations
While basic troubleshooting pressurisation units, and maintenance tasks can be performed in-house, certain situations necessitate the expertise of qualified professionals.
- Complex Diagnostics: If you are unable to identify the root cause of a persistent problem despite following the troubleshooting pressurisation units steps, it's time to call in experts.
- Specialised Repairs: Repairs involving welding, extensive component replacement within the pressurisation unit, or dealing with boiler controls require specialised skills and tools.
- Safety Concerns: If you have any doubts about your ability to safely perform a repair, always err on the side of caution and seek professional assistance.
- Warranty Requirements: Some repairs or modifications might affect the warranty of your equipment, so it's essential to consult with authorised service providers.
National Pumps and Boilers: Your Partner in Heating System Efficiency
At National Pumps and Boilers, we are committed to providing comprehensive support for all your commercial heating needs. Our experienced team possesses the in-depth knowledge and expertise to effectively diagnose and resolve a wide range of pressurisation unit issues. We offer:
- Expert Troubleshooting and Repair Services: Our skilled technicians can quickly identify and rectify problems with your pressurisation units, minimising downtime and ensuring the comfort of your building.
- Preventative Maintenance Programs: We offer tailored maintenance plans designed to keep your heating system operating at peak efficiency and prevent costly breakdowns.
- High-Quality Products and Components: We supply a wide selection of reliable pressurisation units, pumps, expansion vessels, and other essential components from leading manufacturers like Andrews, Ebara, Mikrofill, ATAG, Hamworthy, Stuart Turner, and Keston.
- Comprehensive System Assessments: We can conduct thorough assessments of your heating system to identify potential issues and recommend proactive solutions.
- Dedicated Customer Support: Our friendly and knowledgeable team is always available to provide expert guidance and support.
Taking Control of Your Pressurisation Unit Health
Addressing pressurisation unit issues promptly and implementing a robust preventative maintenance strategy are essential for ensuring the efficient, reliable, and cost-effective operation of your commercial heating system. By understanding the common problems, employing effective troubleshooting pressurisation units techniques, and knowing when to seek professional help from partners like National Pumps and Boilers, you can safeguard your heating infrastructure and maintain a comfortable environment for years to come. Don't wait for a minor issue to escalate into a major problem – reach out to National Pumps and Boilers today to discuss your pressurisation unit needs and explore how we can help you maintain optimal system performance. We are just a click away on our Homepage. You can also explore our range of DHW Pumps, Submersible Pumps, and Shower Pumps for other fluid transfer solutions.