How to Install and Configure a Cold Water Booster System
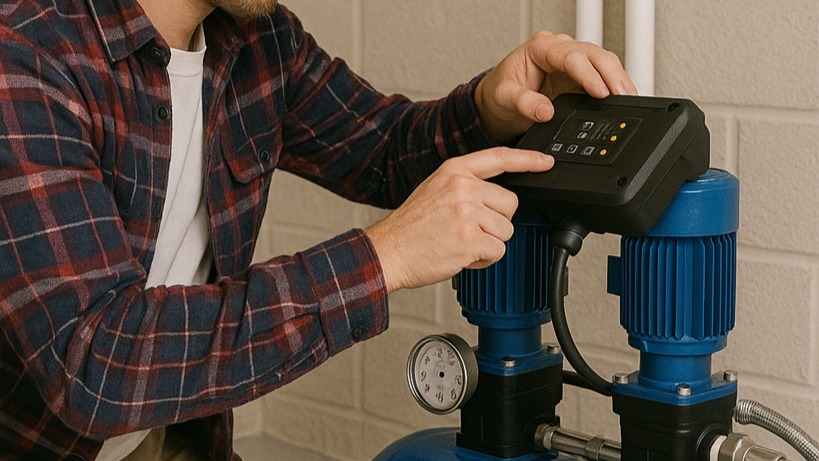
Ensuring a robust and reliable water supply is fundamental to the smooth operation of any commercial building. From hotels needing consistent shower pressure for guests to offices requiring dependable water for restrooms and kitchens, inadequate pressure is simply not an option. Cold water booster systems are the established solution, designed to elevate incoming mains pressure to meet the demands of the building. However, specifying and purchasing the right system is only half the battle. Correct installation and configuration are absolutely critical to achieving the desired performance, ensuring safety, complying with regulations, and maximising the system's lifespan and efficiency. This guide provides an overview of the key stages involved in a professional water booster pump installation and the essential pump setup (commissioning) process, highlighting why expert involvement is crucial for success.
Understanding the System: A Quick Recap
Before delving into installation, let's briefly recall what a cold water booster system comprises. It's an integrated package, typically including:
- Pumps: Usually multi-stage centrifugal pumps designed to generate pressure efficiently. Often installed in multiples (duty/standby or duty/assist) for reliability and efficiency.
- Pressure Vessel(s): Tanks (similar to Expansion Vessels) containing a pressurised air cushion to buffer the system, reduce pump cycling, and smooth pressure delivery.
- Control System: The 'brain', incorporating sensors (pressure transducers), motor starters or Variable Speed Drives (VSDs), protective devices, and control logic, often housed in a dedicated panel.
- Manifolds, Valves & Pipework: Interconnecting pipework (suction and discharge manifolds), isolation valves, check valves (Pump Valves), pressure gauges, and safety valves.
These components work together to draw water from the mains supply (often via a break tank in the UK for regulatory compliance) and deliver it at a consistently higher pressure to the building's distribution network. You can explore various configurations under Pressurisation Units.
Crucial Preparation Before Installation Begins
Thorough preparation is the foundation of a successful water booster pump installation. Rushing this stage inevitably leads to problems down the line. A professional approach involves several key preparatory steps:
Detailed Site Assessment and Survey
This goes far beyond simply checking if the booster set will fit in the plant room. A qualified engineer or surveyor should assess:
- Location Suitability: Is the proposed location adequately ventilated (especially for VSD panels)? Is it protected from frost and excessive heat? Is there sufficient clear space around the unit for safe access during maintenance and repairs?
- Structural Considerations: Can the floor adequately support the weight of the booster set, associated pipework, and the water it contains when operating?
- Noise and Vibration: Will noise or vibration from the operating pumps transmit to occupied areas? Are anti-vibration mounts and flexible pipe connections specified?
- Drainage: Is there adequate drainage nearby for potential leaks or discharge from the pressure relief valve?
- Existing Services: Verification of the incoming water supply pipe size, material, and condition. Detailed assessment of the existing electrical supply – confirming capacity (kW/Amps), voltage, phase, isolation points, and condition of wiring – is critical. The suitability of the existing distribution pipework must also be confirmed.
System Design and Specification Confirmation
Prior to ordering equipment, a detailed design specifying the required duty point (flow and head), pump selection, control strategy (fixed speed or VSD, number of pumps), pressure vessel sizing, pipe sizing, and necessary protection features must be finalised. This ensures the chosen booster set model (e.g., from quality manufacturers like Grundfos, Lowara, or Wilo) is perfectly matched to the building's requirements. National Pumps and Boilers can provide expert assistance in selecting the correct specification.
Gathering Tools, Equipment, and Materials
The installation team must be equipped not only with standard plumbing and electrical tools but also any specialist equipment needed (e.g., heavy lifting gear for large sets, pipe threading/grooving machines, pressure testing equipment). Crucially, all necessary materials – the booster set itself, correctly rated pipework, fittings, valves, cables, containment, fixings, sealants, anti-vibration mounts – must be on site and verified against the specification.
Ensuring Regulatory Compliance (UK Focus)
This is non-negotiable and a key reason why professional installation is essential. Installers must work in accordance with:
- Water Supply (Water Fittings) Regulations 1999: Govern the design, installation, and maintenance of plumbing systems connected to the public water supply. Key aspects include preventing waste, misuse, undue consumption, and contamination (hence the common requirement for break tanks before booster sets) and using WRAS-approved products.
- Building Regulations: Particularly Part G (Water Efficiency, Safety), Part L (Energy Efficiency), and Part P (Electrical Safety).
- Relevant Standards: BS EN 806 and BS 8558 provide detailed guidance on best practices for designing, installing, and maintaining potable water systems within buildings.
- IET Wiring Regulations (BS 7671): The definitive standard for all electrical installation work in the UK.
Attempting a DIY installation without thorough knowledge of these regulations risks non-compliance, potential safety hazards, and invalidating warranties. For advice on selecting compliant products, Contact Us. (Note: This overview is for educational awareness; always consult qualified professionals regarding specific compliance obligations).
The Installation Process: A Professional Overview
The following steps outline the typical process undertaken by qualified engineers during a water booster pump installation. This is not intended as a DIY guide.
Step 1: System Isolation and Preparation
- Safely shut off the incoming mains water supply to the work area using the appropriate isolation valve.
- Implement lock-off/tag-out procedures to prevent accidental reactivation during work.
- Drain down the section of pipework where the new system will be connected, managing the discharged water safely.
Step 2: Positioning and Mounting the Booster Set
- Carefully move the booster set into its designated position, using appropriate lifting equipment if necessary.
- Ensure the unit's baseframe is perfectly level. Shim if required.
- Securely fix the baseframe to the floor using appropriate anchor bolts.
- Install specified anti-vibration mounts between the baseframe and the floor slab to minimise noise and vibration transmission.
Step 3: Connecting System Pipework
- Connect the building's incoming water supply pipework to the booster set's suction manifold.
- Connect the booster set's discharge manifold to the building's distribution pipework.
- Use appropriate fittings (flanges with correct gaskets, unions, adapters) ensuring compatibility between different pipe materials.
- Ensure pipework is correctly aligned to avoid putting stress on the pump or manifold connections.
- Install necessary isolation valves on suction and discharge lines, ensuring they are accessible. Check valves on each pump discharge must be present and correctly oriented.
- Install pressure gauges and any other specified fittings.
- Ensure all pipework is adequately supported independently of the booster set.
Step 4: Pressure Vessel Installation and Pre-Charging
- If the pressure vessel(s) are supplied loose, position and secure them as per the design.
- Connect the vessel(s) to the designated connection point on the booster set pipework.
- Crucially: Before filling the system with water, the installer must check and adjust the air pre-charge pressure within each vessel using a calibrated gauge and pump (e.g., foot pump). The correct pre-charge pressure is determined by the system's operating pressures (typically set slightly below the pump cut-in pressure or minimum system pressure) and is vital for correct operation. Failure to set this correctly is a common cause of problems.
Step 5: Electrical Connections (Qualified Electricians Only)
- This work must be carried out by a competent, qualified electrician adhering strictly to BS 7671 and the manufacturer's wiring diagrams.
- Run appropriately sized power cabling from a suitable, dedicated electrical supply point (with correct isolation and overcurrent protection) to the booster set's control panel isolator.
- Connect power wiring within the panel to the main terminals, VSDs, or motor starters.
- Connect control wiring between the panel and external sensors (pressure transducers, level switches in break tanks).
- Ensure all wiring is correctly terminated, segregated (power vs control), and mechanically protected (e.g., in conduit or trunking).
- Verify that the correct earthing arrangements are in place for safety.
- Perform initial electrical safety checks (insulation resistance, earth continuity).
Step 6: Control System Setup (Initial Power-Up)
- Ensure the control panel enclosure is correctly installed and accessible.
- Connect all internal and external control wiring as per the diagrams.
- Perform initial supervised power-up checks, verifying power indicators, display functionality (if fitted), and absence of immediate electrical faults.
Configuring the System: The Critical Commissioning Phase
Installation lays the groundwork, but commissioning is where the system is fine-tuned and verified – the detailed pump setup. This essential phase should be carried out by engineers with specific expertise in booster sets and control systems, such as the team at National Pumps and Boilers or their approved partners.
Setting Operating Pressures and Control Parameters
- For fixed-speed systems, precisely set the cut-in and cut-out pressure switch points based on design requirements.
- For VSD systems, configure the target pressure setpoint(s), PID control loop parameters (for stable pressure control), acceleration/deceleration ramps (for smooth starts/stops), minimum/maximum speed limits, and any proportional pressure settings required to compensate for friction loss.
Configuring Protection Systems
- Set motor overload protection devices accurately based on the pump motor's full load current rating.
- Configure and test dry run protection function (using level switches, probes, or load monitoring). Adjust sensitivity and timer delays as needed.
- Verify that phase failure protection (for 3-phase systems) is active and correctly configured.
Comprehensive Functional Testing
- Test the manual operation of each pump.
- Verify correct motor rotation direction (for 3-phase pumps).
- Simulate demand changes to test automatic pressure control (fixed speed start/stop sequence or VSD speed modulation).
- Test multi-pump operations: automatic alternation between duty/standby pumps; correct sequencing and speed control in cascade (duty/assist) systems.
- Test all alarm functions (high pressure, low pressure, dry run, pump fault) and verify outputs to BMS or local beacons/sounders if connected.
Hydraulic System Checks
- Slowly fill the system with water, carefully venting air from high points in the pipework and pumps.
- Check the entire system (booster set and connected pipework) thoroughly for leaks under operating pressure.
- Verify stable operating pressure is maintained under varying flow conditions. Measure flow and pressure at key points if instrumentation allows, comparing against design specifications.
- Listen for any unusual noise (e.g., cavitation, bearing noise) or excessive vibration.
Final Checks and Documentation
- Complete a detailed commissioning checklist, recording all final settings, test results, and measurements.
- Ensure all access panels and safety guards are securely refitted.
- Provide the client/facilities manager with a full handover pack including operating & maintenance manuals, wiring diagrams, the commissioning report, and WRAS compliance information (if applicable).
- Provide basic operational training for designated site staff.
Troubleshooting Common Installation & Commissioning Issues
During the pump setup or initial operation, experienced engineers look for common issues:
- Leaks: Often due to improperly tightened fittings, damaged seals, or incorrect jointing methods.
- Incorrect Motor Rotation: Causes low/no flow and potential pump damage (3-phase only). Easily rectified by swapping two phases (by an electrician).
- Air Locking: Air trapped in the pump or pipework preventing proper priming or causing erratic operation. Requires careful venting.
- Incorrect Vessel Pre-charge: Leads to rapid cycling (fixed speed) or pressure instability. Requires correct setting before system pressurisation.
- Control Parameter Mismatch: Incorrect VSD settings or pressure switch levels causing unstable pressure, hunting, or failure to meet demand. Requires expert adjustment.
- Sensor Issues: Faulty or incorrectly installed pressure transducers or level switches giving false readings to the controller.
- Electrical Faults: Tripping breakers/RCDs due to wiring errors, faulty components, or insufficient power supply capacity.
Post-Installation: Handover and Ongoing Maintenance
A professional water booster pump installation concludes with a proper handover.
- Documentation is Key: Ensure you receive and file all manuals, commissioning reports, and diagrams. Understand the basic operation and fault indicators.
- Establish a Maintenance Plan: Based on the manufacturer's recommendations and the commissioning engineer's advice, establish a schedule for routine checks (visual inspections, leak checks, listening for unusual noises) and preventative maintenance (e.g., annual service including vessel pre-charge check, seal inspection, control calibration). National Pumps and Boilers offers comprehensive maintenance contracts.
- Monitor Performance: Keep an eye on system pressure stability and track energy consumption. Significant deviations from the commissioned performance can indicate developing issues requiring attention.
Why Trust National Pumps and Boilers for Installation and Setup?
While this guide outlines the process, the complexity and critical nature of water booster pump installation and pump setup demand professional execution. At National Pumps and Boilers, we offer:
- Expertise: Deep understanding of booster system technology, control strategies, and UK regulations.
- Quality Products: Supply of reliable, efficient booster sets and components from leading Brands.
- Commissioning Services: Our skilled engineers ensure your system is configured correctly for optimal performance, safety, and efficiency.
- Maintenance Support: Tailored service contracts to keep your investment running smoothly for years to come.
- Troubleshooting: Expert diagnostics and repair services if issues arise.
Ready for a Professional Booster System Installation?
Ensuring your cold water booster system is installed and configured correctly is paramount for reliable, efficient, and safe operation in your commercial building. Don't leave it to chance.
If you require a new water booster pump installation, need expert commissioning for a system you've acquired, or seek professional maintenance support, Contact National Pumps and Boilers today. Let our specialists ensure your pump setup delivers the performance and reliability your building demands.