Key Features to Look for When Buying a Cold Water Booster System
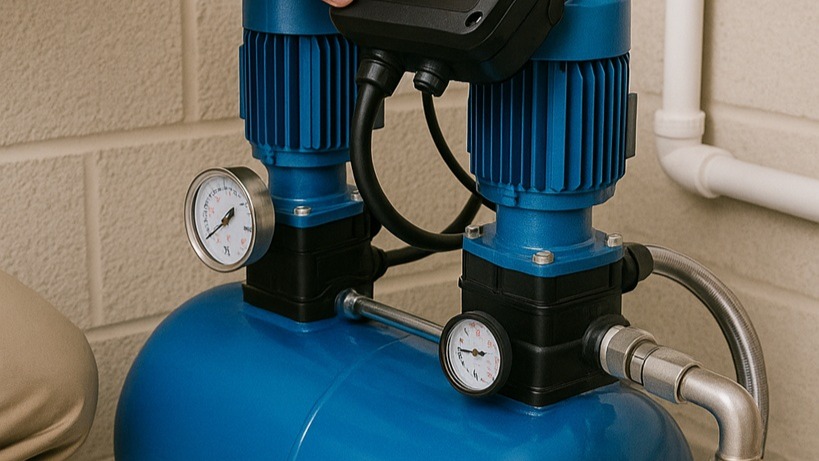
Maintaining adequate and consistent water pressure in any commercial or large residential building is not just a convenience; it's often a necessity. From ensuring hygiene standards in washrooms to facilitating critical processes in healthcare or industrial settings, reliable water flow is paramount. Experiencing a sudden drop in pressure, especially during peak usage times – the frustrating trickle from a tap when multiple outlets are open – is a clear sign that the existing water supply system is inadequate. Investing in a well-specified cold water booster system is the definitive solution to these problems.
However, choosing the right system involves more than just picking a unit off the shelf. Understanding the critical cold water booster features is essential to ensure you select a system that meets your building's specific demands efficiently and reliably for years to come. This guide delves into the essential characteristics and capabilities – the crucial booster pump features and system-wide attributes – you need to evaluate to make an informed purchasing decision, ensuring optimal performance and long-term value aligned with the quality and expertise you'd expect from specialists like National Pumps & Boilers.
Recapping the Role of Cold Water Booster Systems
Before we dissect the specific features, let's briefly revisit why these systems are indispensable in many UK buildings. Municipal water mains pressure, while adequate for smaller dwellings, often falls short in multi-storey buildings due to the vertical height water needs to travel (static head) and pressure losses from friction within extensive pipe networks. Furthermore, commercial buildings typically experience much higher and more concentrated peak water demands than residential homes.
A cold water booster system directly addresses these challenges. It takes the incoming mains water (or water from a break tank) and uses pumps to increase its pressure, ensuring sufficient flow and pressure are available at all outlets, regardless of building height or simultaneous usage. Selecting a system with the appropriate features ensures this crucial function is performed effectively, efficiently, and reliably.
Core Performance Features: The Heart of the System
These features directly relate to the system's primary function: delivering the required amount of water at the right pressure. Getting these wrong can lead to poor performance or inefficiency.
Pump Type and Configuration: More Than Just Moving Water
The pumps are undeniably the core components. Understanding the different types and configurations available is fundamental. These are critical booster pump features to consider:
- Centrifugal Pumps: The vast majority of cold water booster systems utilise centrifugal pumps. These pumps use a rotating impeller to draw water in and 'fling' it outwards at higher velocity and pressure. They are efficient, reliable, and well-suited to the continuous operation often required in boosting applications.
- Multi-Stage Centrifugal Pumps: For applications requiring significant pressure increases (common in taller buildings), multi-stage pumps are the standard. They feature multiple impellers arranged in series within a single pump casing. Each stage adds progressively more pressure, allowing them to achieve high discharge heads efficiently. Leading manufacturers like Grundfos, Lowara, and Wilo offer a wide range of highly reliable multi-stage pumps.
- Vertical vs. Horizontal Configuration: Pumps within a booster set can be mounted either vertically or horizontally.
- Vertical Pumps: Often preferred for their smaller footprint, making them suitable for plant rooms with limited floor space.
- Horizontal Pumps: Can sometimes offer easier access for certain maintenance tasks, though they may require more floor area. The choice often depends on the specific model range and plant room layout. Brands like DAB and Ebara provide options in both configurations.
- Number of Pumps (Simplex, Duplex, Triplex+): Booster sets rarely rely on a single pump (simplex) in commercial settings due to the lack of redundancy.
- Duplex Sets (2 Pumps): Extremely common, offering operational flexibility. They can run in duty/standby mode (one pump operates, the other is a backup, automatically switching over if the duty pump fails or during timed changeovers to equalise wear) or duty/assist mode (one pump handles low flows, the second assists during peak demand).
- Triplex/Quadplex Sets (3 or 4 Pumps): Used for larger buildings with higher flow requirements or a wide variation between minimum and peak demand. They offer greater redundancy and allow for more precise matching of output to demand by staging the pumps.
Flow Rate Capacity (Q): Matching Supply to Demand
This defines the volume of water the system can deliver, typically measured in litres per second (l/s), cubic metres per hour (m³/hr), or gallons per minute (gpm).
- Accurate Sizing is Crucial: The system's flow rate capacity must be sufficient to meet the building's calculated peak demand – the maximum expected simultaneous water usage. This is determined through methods like the fixture unit calculation, analysing building type (offices, hotels, hospitals have different patterns), and occupancy levels.
- Consequences of Incorrect Sizing:
- Undersized: The system cannot cope during peak periods, resulting in pressure drops and inadequate flow at outlets – the very problem it's meant to solve.
- Oversized: Leads to unnecessary initial capital cost, potentially higher energy consumption (especially with fixed-speed pumps), and can cause pumps to operate inefficiently outside their ideal performance range.
- Expert Calculation: Determining the correct flow rate requires careful calculation and understanding of usage patterns. Consulting with specialists, like the team at National Pumps & Boilers, ensures this critical parameter is correctly specified.
Pressure Rating (Head, H): Overcoming Height and Friction
This defines how high or with how much force the system can deliver water, typically measured in bar or metres head (1 bar ≈ 10.2 metres head).
- Components of Pressure Requirement: The required discharge pressure is the sum of:
- Static Head: The vertical height difference between the booster set and the highest outlet point in the building.
- Friction Losses: Pressure lost due to friction as water flows through pipes, bends, valves, and fittings. Longer pipe runs, smaller diameters, and higher flow rates increase friction loss.
- Required Residual Pressure: The minimum acceptable pressure needed at the furthest or highest outlet for fixtures to operate correctly (e.g., 1.5 - 2.5 bar).
- Pump Curve: Manufacturers provide performance curves for each pump model, showing the relationship between flow rate (Q) and pressure/head (H). Selecting a pump or set involves choosing one where the calculated duty point (required Q and H) falls within the pump's efficient operating range.
- Matching to Building: The pressure rating must be sufficient to overcome the building's specific height and pipework layout characteristics while maintaining the desired residual pressure everywhere.
Efficiency and Control Features: Optimising Performance and Costs
Modern booster systems incorporate features designed not just to meet demand, but to do so intelligently and efficiently, saving energy and enhancing reliability. These cold water booster features are increasingly important.
Energy Efficiency: Reducing Costs and Environmental Impact
With rising energy costs and increased environmental awareness, energy efficiency is a paramount consideration.
- Variable Speed Drives (VSDs): This is the single most impactful feature for energy efficiency in booster sets. See detailed section below.
- High-Efficiency Motors: Look for pumps equipped with high-efficiency electric motors conforming to IE3 (Premium Efficiency) or IE4 (Super Premium Efficiency) standards. These motors convert more electrical energy into mechanical power, reducing waste heat and electricity consumption.
- Optimised Pump Hydraulics: Well-designed pump impellers and casings (the 'wet end') minimise energy losses as water passes through. Reputable manufacturers invest heavily in computational fluid dynamics (CFD) to optimise hydraulic efficiency across a wide operating range.
- System Design: Correct pipe sizing within the booster set manifold and the selection of low-loss ancillary components also contribute to overall system efficiency.
- Lifecycle Costing: An energy-efficient system might have a higher purchase price, but the reduction in ongoing electricity bills often results in a lower Total Cost of Ownership (TCO) and a rapid return on the initial investment.
Variable Speed Drives (VSDs): The Smart Energy Saver
VSDs (also known as variable frequency drives or VFDs) are electronic devices that control the rotational speed of the pump's electric motor. Unlike fixed-speed pumps that run at full speed whenever active, VSD-controlled pumps adjust their speed in real-time to precisely match the building's fluctuating water demand.
- How They Work: Pressure sensors monitor the system pressure. If demand increases and pressure starts to drop, the VSD increases pump speed. If demand decreases and pressure rises, the VSD slows the pump down, maintaining a constant pre-set pressure level.
- Major Benefits:
- Significant Energy Savings: Water demand in most buildings varies considerably. By slowing down the pumps during periods of low demand, VSDs dramatically reduce energy consumption. According to the pump affinity laws, power consumption is proportional to the cube of the speed – even a small reduction in speed yields substantial power savings (e.g., reducing speed by 20% can reduce power consumption by nearly 50%).
- Constant Pressure Control: VSDs provide very stable and consistent water pressure, eliminating the wider pressure fluctuations common with fixed-speed systems switching on and off.
- Soft Start/Stop: Gradually accelerating and decelerating the pumps reduces mechanical stress on couplings, seals, and bearings, extending component life. It also minimises electrical current surges during startup and reduces hydraulic shock (water hammer) in the pipework.
- Reduced Noise: Pumps running at lower speeds are inherently quieter.
- The Modern Standard: Due to their significant benefits, VSDs are now considered the standard for most commercial cold water booster applications. When considering booster pump features, the inclusion of VSD technology is often non-negotiable for efficiency and performance.
Control Systems and Intelligence: The Brain of the Booster
The control panel governs the operation of the booster set, monitors its status, and provides essential safety functions. Modern controllers offer sophisticated capabilities:
- Programmable Logic Controllers (PLCs) / Microprocessors: These are the core decision-making units, running algorithms to manage pump operation based on sensor inputs (pressure, flow) and user settings.
- Human-Machine Interface (HMI): A display panel (often touchscreen) allowing users to monitor system status (pressure, pump speed, running hours, energy consumption), adjust settings (set pressure, alarm levels), view fault history, and perform basic diagnostics. User-friendliness is key.
- Advanced Control Logic: Includes features like automatic pump alternation (duty cycling) in multi-pump sets, staged pump operation, anti-seize cycles (briefly running standby pumps), and intelligent responses to fault conditions.
- Connectivity & BMS Integration: Many controllers offer communication ports (e.g., Modbus, BACnet, Ethernet/IP) allowing integration with a central Building Management System (BMS) for remote monitoring, control, and data logging.
- Comprehensive Protection: Essential safety functions include:
- Dry Run Protection: Detects loss of incoming water supply and stops the pumps to prevent damage.
- Overload Protection: Protects motors from excessive current draw.
- Over/Under Voltage Protection: Safeguards against damaging power supply fluctuations.
- High/Low Pressure Alarms: Alert operators to abnormal system pressure conditions.
Durability and Build Quality Features: Ensuring Longevity
A cold water booster system is a significant investment expected to provide reliable service for many years. Features related to construction and materials are critical for longevity and dependable operation.
Materials of Construction: Resisting Wear and Corrosion
The materials used for components in contact with water ('wetted parts') and structural elements significantly impact durability.
- Pump Casings & Impellers:
- Stainless Steel (e.g., Grades 304, 316): Offers excellent corrosion resistance, ideal for potable water, hygienic, smooth surfaces contributing to efficiency. Often the preferred choice for high-quality systems.
- Cast Iron: Robust and cost-effective, often used for pump casings and baseplates. May require internal coatings or specific grades for potable water use.
- Manifolds: Typically stainless steel for durability and hygiene in potable water systems.
- Valves: Bodies often made of brass, bronze, ductile iron, or stainless steel. Ensure compatibility with potable water. See our range of reliable Pump Valves.
- Pressure Vessels: Usually steel shells with internal bladders or diaphragms made from potable water-approved elastomers (e.g., EPDM). Quality vessels from brands like Reflex or Flamco ensure long life.
- WRAS Approval: Crucially, for any system supplying drinking water in the UK, all materials in contact with the water MUST be WRAS (Water Regulations Advisory Scheme) approved. This ensures materials are safe and do not contaminate the water supply. Always verify WRAS certification for the complete booster set.
Build Quality and Assembly: The Foundation of Reliability
Beyond individual component materials, the overall assembly quality matters.
- Robust Base Frame: A sturdy, often powder-coated or galvanised steel base frame ensures components are securely mounted, aligned, and vibration is minimised.
- Quality Pipework & Welding: Professionally constructed manifolds with high-quality welds or fittings prevent leaks and ensure hydraulic efficiency.
- Anti-Vibration Mounts: Effective rubber or spring mounts between the base frame and the floor (or integral to the pump/motor assembly) prevent operational noise and vibration from transmitting into the building structure.
- Factory Testing: Reputable manufacturers test assembled booster sets before despatch to verify performance, check for leaks, and ensure control systems function correctly. Our own NPB-branded booster sets are assembled with meticulous attention to quality.
Environmental Protection Features: Surviving the Elements
Consider where the booster set will be installed.
- IP Rating (Ingress Protection): Indicates the level of protection electrical enclosures (like control panels and motor terminal boxes) offer against dust and water ingress. Higher ratings (e.g., IP55, IP65) are needed for damp or dusty environments.
- Weatherproof Enclosures: For outdoor installations, fully weatherproof and potentially insulated enclosures are required to protect components from rain, sun, and temperature extremes.
- Frost Protection: In unheated locations susceptible to freezing, trace heating on pipework and pumps, or thermostatically controlled heaters within enclosures, are essential to prevent damage.
Installation, Maintenance, and Support Features
Ease of installation (for professionals), straightforward maintenance, and available support significantly impact the overall ownership experience.
Features Facilitating Installation and Space Planning
- Compact Design: Especially important in retrofit situations or small plant rooms. Vertical pump configurations often contribute to a smaller footprint.
- Clear Connection Points: Well-labelled and accessible suction and discharge connection points simplify pipework installation.
- Lifting Points: Integrated lifting eyes or points on the base frame facilitate safe handling and positioning.
- Comprehensive Documentation: Clear installation manuals, wiring diagrams, and commissioning guides are essential for installers.
Features Enhancing Maintainability
- Accessible Components: Design that allows easy access to pumps, motors, seals, pressure vessels (especially the air valve for pre-charge checks), and control panels simplifies inspection and servicing.
- Isolation Valves: Integral isolation valves for each pump and the main inlet/outlet allow individual components or the whole set to be isolated for maintenance without draining large sections of pipework.
- Easy-to-Clean Strainers: If inlet strainers are fitted, they should be easily accessible for cleaning.
- Diagnostic Aids: Control panels with clear fault diagnostics and event logs help technicians quickly identify and resolve issues.
- Spares Availability: Choosing systems from established manufacturers supplied by reputable distributors like National Pumps & Boilers ensures better long-term availability of spare parts (seals, bearings, control components, etc.).
Warranty and Supplier Support: Peace of Mind
- Warranty Period: Check the manufacturer's warranty duration for different components (pumps, motors, VSDs, vessels, and controls often have varying warranties).
- Supplier Expertise: Partnering with a supplier who understands the products technically can be invaluable for troubleshooting and advice.
- Service Agreements: Consider ongoing service agreements for planned preventative maintenance by qualified engineers to ensure optimal performance and longevity.
For any support needs or inquiries about maintenance, feel free to reach out via our Contact Page.
Budget Considerations: Balancing Cost and Value
While features drive performance, budget is always a factor.
Initial Cost vs. Total Cost of Ownership (TCO)
Avoid selecting solely on the lowest purchase price. A cheaper, less efficient fixed-speed system or one with lower build quality might save money upfront, but cost significantly more over its lifetime due to:
- Higher energy bills.
- More frequent breakdowns and repairs.
- Shorter operational lifespan, requiring earlier replacement.
Evaluate the TCO, considering the initial investment plus projected energy and maintenance costs over the system's expected life. High-quality, efficient systems often provide better long-term value.
Comparing Quotes Effectively
When you decide to buy pressure pump systems and are comparing quotes, ensure they detail all the key cold water booster features discussed here (pump type/number, VSD, motor efficiency, materials, control features, warranty) so you can compare like-for-like value, not just the bottom-line price.
Why Choose National Pumps and Boilers?
At National Pumps and Boilers, we understand the importance of every feature. We don't just sell boxes; we provide solutions.
- Expert Guidance: We help you navigate the complexities of booster pump features to select the system perfectly matched to your requirements.
- Quality Brands: We supply systems featuring components from trusted manufacturers renowned for quality and reliability, including Grundfos, Lowara, Wilo, and more.
- Tailored Solutions: From standard sets to bespoke configurations, we ensure you get the right fit.
- Comprehensive Support: Our commitment extends beyond the sale, offering technical support and access to spares.
Making the Right Choice for Your Building
Selecting a cold water booster system is a critical infrastructure decision. By carefully evaluating the key cold water booster features – from core performance metrics like flow and pressure, efficiency enhancements like VSDs, through to durability, controls, and maintainability – you can ensure you invest in a system that delivers reliable, efficient performance for the long term. Understanding these essential booster pump features empowers you to ask the right questions and make a choice that provides true value.
Ready to discuss your specific requirements or need assistance selecting a cold water booster system with the right features for your building? Explore our range and expertise on our Homepage or get in touch directly via our Contact Page. Let National Pumps & Boilers help you secure a dependable water supply.