Troubleshooting Common Problems with Andrews Water Heaters
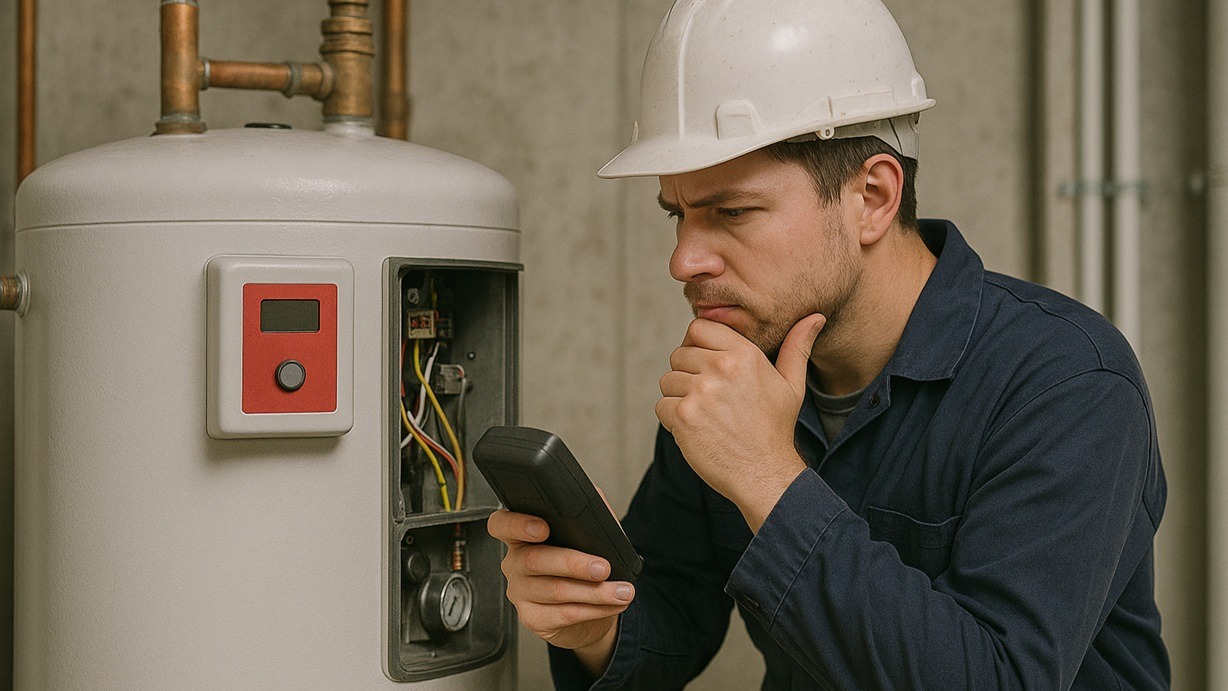
Even with a well-maintained system, water heaters can occasionally run into issues. Whether you're operating a busy hotel, healthcare facility, or leisure centre, quick problem resolution is essential to avoid operational disruption. Fortunately, Andrews water heaters are designed with durability and ease of service in mind. Understanding the most common water heater troubleshooting problems can help you address faults quickly and effectively. In this guide, we’ll explore Andrews water heaters technical concerns, causes, and tips for getting your system back on track.
Diagnosing Common Andrews Water Heater Faults
Commercial environments demand consistent hot water. When something goes wrong, pinpointing the issue early can prevent a minor fault from turning into a costly repair. Here are the most frequently encountered issues and how to tackle them:
1. No Hot Water
This is one of the most common complaints and can stem from several issues:
- Faulty thermostats
- Ignition failure (in gas units)
- Tripped safety cut-out switches
- Pilot light outage
Troubleshooting tip: Start by checking the unit’s display panel for fault codes. Reset the cut-out switch if it is safe to do so. If the pilot won't relight or the ignition fails repeatedly, a professional inspection may be required.
2. Inconsistent Water Temperature
Fluctuating water temperatures may indicate:
- Thermostat malfunction
- Limescale build-up on heat exchangers
- Flow rate inconsistencies
Technical insight: Build-up of scale reduces heat transfer efficiency. Flushing the system or descaling components can help restore temperature stability. This is especially important in hard water regions.
3. Low Water Pressure or Flow
Reduced flow can impact operations significantly in commercial setups. Causes include:
- Blocked filters or valves
- Air in the system
- Pump failure or incorrect pump settings
Troubleshooting tip: Ensure that pump valves and DHW pumps are functioning properly. Airlocks can sometimes be resolved by bleeding the system.
4. Strange Noises from the Unit
Gurgling, banging, or hissing sounds often signal internal issues:
- Sediment build-up in the tank
- Air in the system
- Scale on heating elements
Solution: A full flush of the tank and pipework may eliminate the problem. If the noise persists, a component inspection is advised.
5. Leaks or Drips
Visible leaks should be addressed immediately to prevent damage. Common causes include:
- Corroded pipework or tank fittings
- Faulty TPR valves
- Excess system pressure
Fix tip: Examine the TPR valve and expansion vessels to ensure the pressure is properly regulated. Tighten or replace worn fittings as needed.
Andrews Water Heaters Technical Error Codes
Modern Andrews systems feature fault displays to simplify diagnostics. While codes vary by model, common indicators include:
- E01/E02: Ignition failure or flame detection fault
- E13: Flue sensor fault
- E28: Overheat or high-limit thermostat triggered
- E43: Pump or circulation error
Pro tip: Always refer to the manufacturer manual or consult with National Pumps and Boilers for accurate interpretation of error codes and professional assistance.
Additional diagnostic indicators
Besides coded faults, look out for visual indicators such as flashing lights, fluctuating pressure gauges, and beeping alarms. Many of these warnings can provide early clues before a full shutdown occurs.
Preventative Measures to Minimise Faults
Troubleshooting is important, but prevention is even better. Consistent system maintenance helps eliminate the root causes of many issues. Here’s what to prioritise:
- Schedule regular flushing to prevent sediment accumulation
- Inspect sensors, thermostats, and safety valves
- Check commercial circulators to maintain system flow
- Test water pressure and regulate it with pressurisation units
- Book an annual inspection with a qualified engineer
Routine checks worth implementing
Implementing weekly visual checks, monthly valve inspections, and quarterly water quality assessments builds a robust maintenance framework. These smaller intervals help identify irregularities that often precede major failures.
When to Call a Professional
While some basic issues can be resolved in-house, others should only be addressed by qualified technicians. Situations that call for expert attention include:
- Repeated ignition failure
- Gas or carbon monoxide alarm triggers
- Persistent leaks
- Frequent cut-out or reset events
- Electrical faults or wiring concerns
National Pumps and Boilers offers specialist support for all Andrews models. Their engineers are well-versed in Andrews water heaters technical specifications and can quickly identify and resolve even complex issues.
Partnering with a reliable service provider
Establishing a long-term relationship with a specialist like National Pumps and Boilers ensures prompt attention in the event of an emergency, whether it’s a fault code you don’t recognise or a component replacement. Timely expertise prevents prolonged disruptions.
The Role of System Compatibility
Using mismatched components or retrofitting incompatible parts can introduce new problems. Ensure that any upgrades or replacements match the heater's performance profile. Stick with trusted brands and products from the same supply network. This includes:
- Compatible thermostats and sensors
- Adequate circulation equipment
- Proper pressure control systems
For integrated solutions tailored to Andrews units, National Pumps and Boilers provides a full range of parts and systems. View their full Andrews water heaters range for compatible products.
Integration for smoother operation
Proper integration with Building Management Systems (BMS) or smart control panels not only improves diagnostics but also helps isolate problems early. Ensure your heating setup communicates effectively across components to streamline system management.
Educating Your Maintenance Team
Empowering your team with troubleshooting knowledge pays dividends. Staff who understand the signs of mechanical failure can act quickly, reducing reliance on external support for simple issues.
Consider providing access to:
- Quick-reference fault guides
- Basic training on system resets
- Step-by-step guides for flushing or bleeding systems
These small interventions promote safety, save time, and ensure your water heater runs at its best throughout the year.
Encouraging proactive reporting
Foster a culture where unusual sounds, inconsistent temperatures, or pressure fluctuations are reported immediately. Early reporting shortens the time between fault development and repair, preventing further system strain.
Final Thoughts
Water heater troubleshooting problems can range from minor inconveniences to serious operational threats. By understanding the typical issues associated with Andrew systems and knowing when to call in support, you can minimise downtime and protect your investment.
Proactive management and technical insight are key. Whether you’re running a care home, university, or industrial site, Andrews water heaters provide the performance and serviceability required in demanding commercial settings.
For expert guidance, support, and replacement parts, reach out to National Pumps and Boilers today. With proper troubleshooting knowledge and responsive technical assistance, your heating system will stay running smoothly, just as it should.