Troubleshooting Common Problems with Commercial Circulators
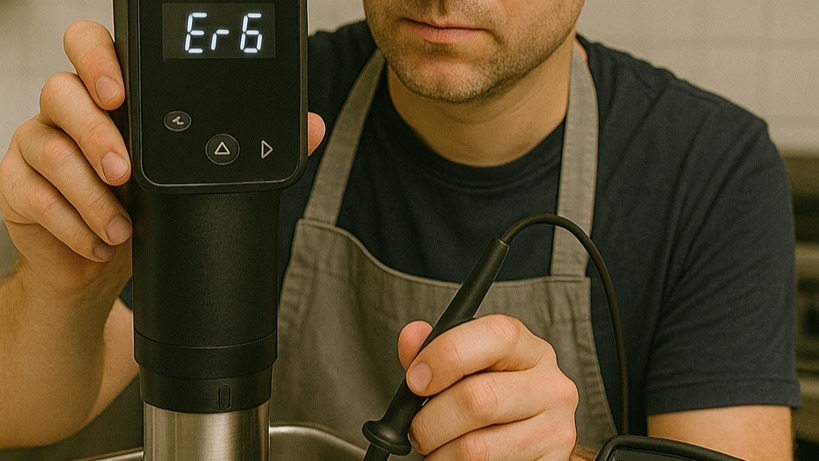
Commercial circulators are the unsung heroes of heating, cooling and hot water systems in hospitals, hotels, schools and office complexes. Yet even the most robust pumps can develop circulator issues over time. Fortunately, many faults are straightforward to diagnose and rectify with a little pump troubleshooting, helping you maintain system efficiency and avoid costly downtime. This complete guide will walk you through the most frequent problems, what causes them, how to identify them and practical steps to fix them, so you can keep your circulator running at peak performance.
Introduction: Understanding Circulator Issues
Commercial circulators move fluid through closed-loop systems, ensuring consistent temperature control and hot water delivery. When they fail or underperform, the consequences can include:
- Reduced occupant comfort
- Increased energy consumption
- Unplanned maintenance costs
- Potential disruption of critical services
Early detection and methodical troubleshooting are key. Whether you manage a hospital boiler room or oversee an educational campus, these techniques will empower your team to tackle common circulator faults confidently.
Why Prompt Troubleshooting Matters
- Operational continuity: In mission-critical environments, even brief outages can pose safety or compliance risks.
- Cost savings: A well-functioning pump minimises electricity draw and prevents collateral damage to boilers, chillers or associated plant.
- Extended equipment life: Addressing wear early prevents minor issues from escalating into major failures.
- Warranty compliance: Leading brands such as Grundfos and Lowara require documented maintenance and fault-finding to uphold warranty terms.
Ready to dive in? Let’s start by checking the power supply.
Diagnosing Power and Control Failures
A circulator that refuses to run is one of the most obvious, and easily preventable, faults. Follow these steps to isolate electrical or control-related issues:
Checking the Electrical Supply
- Verify incoming voltage at the motor control centre or fused switch.
- Inspect breakers and fuses, replace any tripped breakers or blown fuses.
- Confirm isolation switches are in the correct position, following your site’s lock-out/tag-out procedures.
Tip: Clearly label all breakers and fuses connected to your circulator to simplify future fault finding.
Inspecting Wiring and Connections
- Examine cable insulation for cuts or heat damage.
- Tighten terminal screws in the motor junction box, vibrations can loosen connections over time.
- Look for moisture ingress around cable glands, which may cause short circuits.
Testing Motors and Control Electronics
If the supply and wiring check out, the fault may lie in the motor windings or variable-speed drive (VSD):
- Use a megohmmeter to test motor winding insulation resistance.
- Inspect VSD error codes or fault indicators.
- Reset and reprogramme smart control modules, ensuring parameters match your system design.
For complex control faults, our team is always on hand via the contact page to help you configure drives and BMS integration.
Identifying and Resolving Noise and Vibration
Unusual sounds or excessive vibration typically signal underlying mechanical issues. Here’s how to pinpoint and resolve them:
Air Entrapment and Gurgling
- Symptoms: Banging, gurgling or water-hammer noises.
- Cause: Air bubbles trapped in the pump or at high points in the loop.
- Solution:
- Bleed air via the pump’s air-vent screw and bleed valves on radiators or pipe high points.
- Repeat until the noise subsides and flow stabilises.
- Bleed air via the pump’s air-vent screw and bleed valves on radiators or pipe high points.
Bearing Wear and Grinding
- Symptoms: Grinding, whining or loud motor noise.
- Cause: Worn bearings or debris in the bearing housing.
- Solution: Schedule pump troubleshooting with a qualified technician to replace bearings and inspect the shaft for scoring.
Misalignment and Vibration
- Symptoms: Excessive rumbling or shaking during operation.
- Causes: Misaligned pipework, loose mounting bolts or an imbalanced impeller.
- Remedies:
- Tighten all pump foundation and pipe clamp bolts to the manufacturer’s torque specifications.
- Install anti-vibration mounts under the pump base.
- Check impeller clearance and rebalance or replace the impeller if necessary.
- Tighten all pump foundation and pipe clamp bolts to the manufacturer’s torque specifications.
Learn more about vibration reduction in our commercial circulators range.
Detecting and Repairing Leaks
Water pooling around your circulator may indicate seal or gasket failure, corrosion or loose fittings. Leaks not only waste water but also promote corrosion of pump casings and nearby pipework.
Worn Seals and Gaskets
- Symptoms: Drips around the pump casing or flange joints.
- Cause: Mechanical seals and gaskets degrade over time.
- Solution:
- Isolate and drain the circuit.
- Remove the old seal or gasket.
- Clean flange faces thoroughly.
- Fit OEM-specified seals or gaskets, torquing bolts in a star pattern.
- Isolate and drain the circuit.
Corrosion-Related Leaks
- Symptoms: Rust staining, pitting on the housing or visible metal decay.
- Cause: Chemical attack or prolonged moisture exposure.
- Solution:
- Assess severity; minor pitting can be sealed, but extensive corrosion often requires pump replacement.
- Improve plantroom conditions by relocating the pump or installing a pressurisation unit to keep the loop dry when idle.
- Assess severity; minor pitting can be sealed, but extensive corrosion often requires pump replacement.
Loose Fittings
- Symptoms: Intermittent dampness around connections.
- Cause: Vibration-loosened unions or flanges.
- Solution: Hand-tighten fittings, then finish with a torque wrench. Apply thread sealant tape or liquid PTFE where appropriate.
For gasket supplies and accessories, visit our pump valves section.
Addressing Overheating and Blockage Problems
An overheating circulator risks seal failure, motor burnout and unexpected downtime. Keep temperatures in check with these steps:
Blocked Impellers and Strainers
- Symptoms: Pump housing is excessively hot; flow rate drops.
- Cause: Debris, scale or foreign objects obstructing water passage.
- Solution:
- Isolate and dismantle the pump.
- Remove and inspect the impeller for blockages or wear.
- Clean the impeller, volute and suction strainers thoroughly.
- For heavy scale, consider a loop-wide chemical descaling treatment.
- Isolate and dismantle the pump.
Ventilation and Clearance
- Symptoms: Motor overheats despite clean hydraulics.
- Cause: Confined installation or obstructed ventilation.
- Solution:
- Ensure a minimum 300 mm clearance around the pump for air circulation.
- Install ventilation grilles or a small extractor fan if necessary.
- Ensure a minimum 300 mm clearance around the pump for air circulation.
Thermal Safeguards
- Fit temperature sensors on the motor housing to detect rising temperatures early.
- Use thermal imaging during routine checks to spot hotspots before failure.
- Install thermal cut-out switches to shut down the pump if it exceeds safe operating temperatures.
Managing Flow and Pressure Anomalies
Irregular flow or pressure imbalances can disrupt system balancing, leading to hot or cold spots in different zones.
Inconsistent Flow Rates
- Symptoms: Fluctuating readings on flow meters or gauges.
- Causes: Airlocks, partial blockages or impaired impeller performance.
- Solution:
- Re-bleed the system thoroughly.
- Inspect and clean Y-filters or suction strainers on the DHW pumps.
- Compare current flow rates against commissioning data and adjust balancing valves.
- Re-bleed the system thoroughly.
System Pressure Drops
- Symptoms: Loop pressure falls below design set-points.
- Causes: Leaks, valve failures or excessive friction losses.
- Solution:
- Check expansion vessels for leaks or loss of charge.
- Verify that zone valves are operating smoothly.
- Consider uprating pipe diameters if friction losses are excessive.
- Check expansion vessels for leaks or loss of charge.
Impeller Wear
- Symptoms: Steady decline in peak flow or head.
- Cause: Erosion or cavitation pitting on impeller surfaces.
- Solution: Replace the impeller or cartridge assembly. Upgrading to a wear-resistant impeller material can extend service life where fluid abrasives or high mineral content are present.
Dealing with Constant Operation and Control Malfunctions
A circulator that never stops running wastes energy, stresses components and masks other faults.
Thermostat and Sensor Issues
- Symptoms: The Pump runs continuously regardless of demand.
- Causes: Faulty thermostat, incorrect set-points or sensor failure.
- Solution:
- Check thermostat wiring and calibration.
- Replace ageing or malfunctioning temperature sensors.
- Adjust control logic to include proper on/off differentials.
- Check thermostat wiring and calibration.
Control Panel and BMS Faults
- Symptoms: The Pump ignores off-commands from the Building Management System.
- Causes: Communication errors or software glitches.
- Solution:
- Verify network connections (Modbus, BACnet).
- Update firmware on VSDs and smart drives.
- Reload correct parameter sets or consult your BMS integrator.
- Verify network connections (Modbus, BACnet).
Sizing and Duty Checks
- Symptoms: Frequent cycling or laboured operation.
- Cause: Incorrectly sized pump or system volume.
- Solution:
- Review your pump curve against actual system demands.
- Consider upgrading to a higher-capacity model from our Commercial Circulators range.
- For large systems, implement a parallel duty-standby arrangement for load sharing.
- Review your pump curve against actual system demands.
Proactive Maintenance to Prevent Circulator Issues
While pump troubleshooting is invaluable, preventing faults before they occur is even better. Implement this structured regime:
Routine Inspection Checklist
- Visual check for leaks, corrosion and loose fittings.
- Acoustic scan for unusual noises or vibrations.
- Electrical inspection: tighten terminals and perform insulation tests.
- Compare flow and pressure readings with baseline commissioning data.
Cleaning and Lubrication
- Wipe down external motor and pump housings to prevent dust buildup.
- Clear suction strainers and Y-filters on a quarterly basis.
- Lubricate bearings or shafts per manufacturer guidelines (e.g., Wilo, EBARA).
- Replace seals and gaskets every 2–3 years, depending on operating conditions.
Smart Monitoring Integration
Modern circulators with built-in sensors can deliver real-time data on:
- Vibration levels
- Motor current draw
- Bearing and casing temperatures
Our smart monitoring solutions integrate seamlessly with your BMS, providing alerts long before a minor anomaly becomes a major failure.
When to Seek Professional Pump Troubleshooting Services
Some circulator issues demand specialist expertise and tooling. Contact a professional if you encounter:
- Complex electrical faults that basic checks don’t resolve
- Persistent or worsening vibration after initial remedies
- Extensive corrosion or pitting affecting multiple components
- Recurring flow and pressure issues despite routine maintenance
Our certified technicians carry factory-approved spares for brands such as DAB, Armstrong and NPB, ensuring rapid on-site repair and minimal disruption.
Balancing Repair Versus Replacement
- Repair if downtimes are rare and parts remain available.
- Replace if failures are frequent, parts are obsolete, or the pump is more than ten years old.
Upgrading to a modern, high-efficiency circulator often pays back through lower energy bills and reduced maintenance.
Why Choose National Pumps and Boilers
At National Pumps and Boilers, we combine decades of industry experience with the latest diagnostic tools to deliver fast, reliable pump troubleshooting services:
- 24/7 emergency support to minimise downtime
- Fully equipped service vehicles stocked with common spares
- Multi-brand expertise, covering Andrews, Atag, Flamco, Hamworthy, Keston, Mikrofill, Remeha, Reflex, Stuart-Turner, Vaillant and more
- Smart monitoring solutions for proactive fault detection
- Transparent reporting with digital logs of all works carried out
Whether you’re facing a tricky circuit fault or aiming to optimise system reliability, our expert team is ready to help.
Next Steps and Contact Information
Don’t let minor faults evolve into major headaches. Effective pump troubleshooting and proactive maintenance are key to ensuring reliable, energy-efficient operation for years to come.
📞 Contact us today to schedule an inspection, discuss a maintenance contract or arrange emergency repairs. Explore our full range of commercial circulators and related services on the homepage. Let National Pumps and Boilers be your partner in peak performance.