Troubleshooting Vaillant Commercial Boilers: Common Issues and Solutions
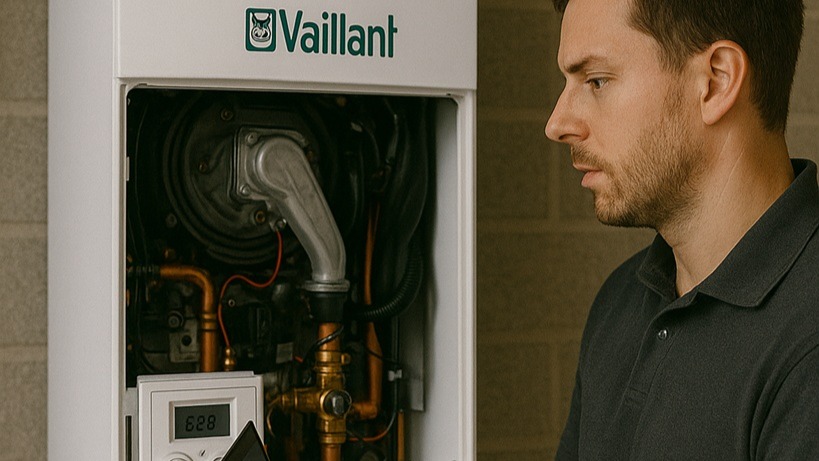
No boiler system is entirely immune to faults, especially in high-demand commercial environments. Even with a reliable, energy-efficient model like a Vaillant, minor issues can occasionally arise. When they do, it’s important to know how to respond effectively without compromising system performance or safety.
This guide focuses on Vaillant boiler troubleshooting for commercial systems, highlighting common boiler faults, their likely causes, and practical steps you can take to resolve them. Whether you’re a facilities manager, building engineer, or service contractor, you’ll find the insights here helpful in minimising downtime and keeping your heating systems running smoothly.
Why Vaillant Boilers Are Trusted in Commercial Settings
Vaillant is a leader in modern condensing technology and efficiency-focused design. Their commercial boilers, available in both wall-hung and floor-standing models, are equipped with high modulation ratios, stainless steel heat exchangers, and advanced control systems.
These features allow them to adapt to changing load demands while delivering steady performance, but like all machines, they still require regular attention and quick action when issues arise.
Common Boiler Faults and How to Troubleshoot Them
Understanding the most frequent issues that arise with commercial boilers can save time and avoid costly service interruptions. Below are the most common boiler faults you might encounter with a Vaillant system and guidance on how to address them.
1. Low System Pressure (F.22 or F.75 Fault Code)
Symptoms: Boiler locks out, poor heat delivery, hissing sounds in pipework.
Likely Cause:
- Leaking pipework or valves
- Air in the system
- Failing expansion vessel
- Faulty pressure sensor (especially in F.75 errors)
Solution:
- Repressurise the system using the filling loop
- Bleed radiators and system loops
- Check for leaks and repair if found
- Inspect or replace the expansion vessel
Consistently low pressure is a sign of an underlying issue, don’t simply reset and repressurise without identifying the root cause.
2. Ignition Failure (F.28 or F.29)
Symptoms: The Boiler will not start or fires intermittently.
Likely Cause:
- Blocked or frozen condensate pipe
- A faulty gas valve or ignition electrode
- Gas supply disruption
Solution:
- Thaw frozen condensate pipe (if external)
- Inspect ignition electrodes for carbon buildup
- Confirm the gas supply is stable and sufficient
- Contact a qualified engineer to test the gas valve
3. Circulation Issues (F.83 or F.84)
Symptoms: Boiler overheating, radiators cold at the bottom, error codes related to flow and return sensors.
Likely Cause:
- Faulty or incorrectly fitted sensors
- Airlock or blockage in the system
- Pump failure
Solution:
- Bleed the system thoroughly
- Flush the system if necessary
- Inspect and replace faulty flow/return sensors
- Upgrade or replace the commercial circulator if it's underperforming
Sensor errors can result from temperature differentials that exceed safe operational limits, often a symptom of deeper circulation problems.
4. Hot Water Inconsistencies
Symptoms: Intermittent hot water or fluctuating temperatures
Likely Cause:
- Failing DHW pump
- Blocked plate heat exchanger
- Incorrect flow rate or temperature setting
Solution:
- Inspect DHW pump performance
- Decalcify or replace the heat exchanger if it is fouled
- Adjust temperature settings on the control interface
Consistency issues in domestic hot water are common in ageing systems or those without proper routine maintenance.
5. Flue Blockage or Ventilation Issue (F.32 or F.33)
Symptoms: The Boiler shuts down unexpectedly or displays airflow-related faults
Likely Cause:
- Blocked flue or air intake
- Broken fan or wiring fault
- Improper flue installation
Solution:
- Inspect the flue outlet for debris or obstructions
- Ensure terminal positioning complies with guidelines
- Check fan operation and replace it if necessary
- Use only certified parts to avoid compatibility issues
6. Boiler Lockouts Due to Temperature Spikes
Symptoms: Boiler locks out intermittently, particularly during startup
Likely Cause:
- Faulty thermostats
- Poor circulation
- Incorrectly set temperature controls
Solution:
- Reset and reconfigure thermostat limits
- Ensure all zones are adequately balanced
- Verify that circulation pumps are not undersized
Addressing lockouts early prevents wider system stress, which can trigger safety shut-offs or component failure.
Preventive Measures for Avoiding Common Faults
Schedule Regular Maintenance
Routine inspections and cleaning help prevent many common issues. Tasks such as flushing the system, checking sensor function, and inspecting the burner should be part of annual servicing. Explore full-service options via our commercial boiler services.
Monitor Water Quality
Poor water quality leads to corrosion, sludge build-up, and sensor malfunctions. Ensure inhibitor levels are maintained, and filters are cleaned regularly.
Install Smart Monitoring Tools
Integrating your Vaillant boiler with a Building Management System (BMS) or digital controller enables real-time fault alerts, performance tracking, and system optimisation.
Ensure Proper Sizing and Installation
Many faults originate from poor initial setup. Oversized boilers short-cycle, while undersized units overwork. Proper sizing and zoning strategies during installation reduce long-term faults.
Understanding Vaillant Fault Codes
Vaillant boilers use a smart diagnostic system that displays error codes when issues arise. Here are a few more important ones to recognise:
- F.20: Overheating
- F.24: Dry fire or pump failure
- F.61: Gas valve fault
- F.64: Electronics fault
- F.76: Overheating of primary heat exchanger
Each of these may relate to circulation problems, poor water flow, or sensor failure. Never ignore these alerts, early action prevents greater damage.
Real-World Case Example: Large Office Complex
A commercial office block in London experienced ongoing issues with inconsistent heating across its top floors. Error logs showed F.83 codes recurring during morning startup.
Our technicians discovered an airlock in one of the return loops and an undersized circulator. Once the loop was bled and a correctly rated Wilo commercial circulator was installed, the issue was resolved. Efficiency improved by 14%, and the heating complaints stopped entirely.
Another example involves a leisure centre experiencing frequent boiler lockouts during peak hours. After inspecting the control settings and system layout, we found the boilers were operating above design temperature due to mismatched setpoints. Adjusting the settings and replacing a faulty flow sensor brought the system back to full functionality.
Tools and Components That Support Boiler Performance
In addition to routine servicing, upgrading system components can improve fault tolerance and prevent common issues:
- Pump valves protect pumps from pressure imbalances
- Submersible pumps support water delivery in specialist applications
- Pressurisation units maintain ideal operating pressure without manual intervention
Using the right components reduces operational strain and makes troubleshooting more straightforward. Ensuring component compatibility with Vaillant systems also avoids false fault codes and sensor errors.
When to Call for Expert Help
Some faults, such as gas-related issues, system wiring, or sensor calibration, should only be handled by qualified professionals. If repeated resets don’t solve the issue, or if you’re unsure of the underlying cause, reach out to the experts at National Pumps and Boilers via our contact page.
Timely intervention from specialists can prevent small issues from escalating into major repairs or system downtime.
Final Thoughts: Stay Ahead of Boiler Issues
Boiler faults don’t have to result in panic or prolonged downtime. With a structured approach to Vaillant boiler troubleshooting, precise knowledge of common boiler faults, and proactive servicing, your commercial heating system can continue to deliver safe, efficient performance year-round.
At National Pumps and Boilers, we’re here to support your commercial heating systems with quality products, responsive servicing, and expert advice.
From essential components to diagnostic assistance, let us help you keep your Vaillant system running exactly as it should.