Upgrading Your Commercial Central Heating System: What to Consider
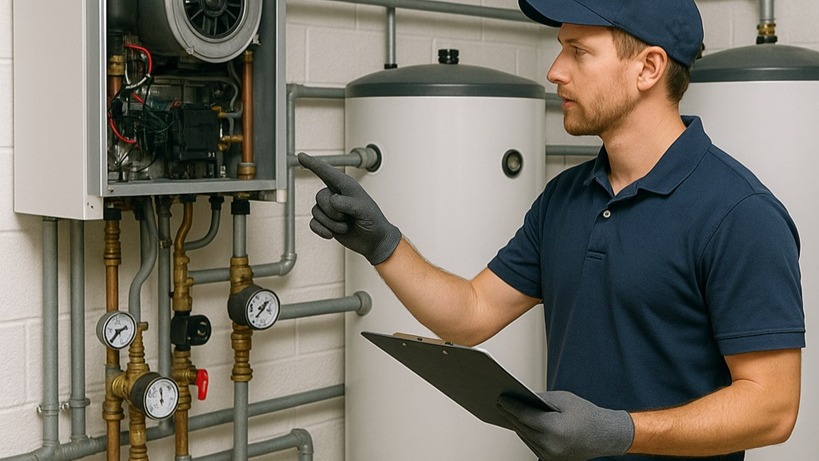
Upgrading your commercial premises’ heating isn’t just a reactive fix; it’s a strategic investment that enhances comfort, lowers running costs and delivers long-term reliability. Whether you’re planning to upgrade central heating in an office block, retail centre or warehouse, thoughtful preparation and professional guidance will ensure your heating system upgrade pays dividends for years to come.
Assessing Your Current System
Before diving into new equipment, conduct a thorough review of your existing setup. Understanding its limitations and performance will inform the scope of your upgrade.
Reviewing System Performance
- Heat-up times: Note if certain zones take significantly longer to reach the set temperature.
- Temperature consistency: Identify cold spots or overheating areas.
- Breakdown history: Collate repair records over the last two to three years.
- Energy bills trend: Compare seasonal usage to detect creeping inefficiencies.
Surveying Plantroom Layout
Inspect the boiler, pumps and ancillary equipment. Age, footprint and condition of pipework will influence whether you can install replacements in the same location or need a plantroom reconfiguration.
For a professional survey and bespoke advice, visit our contact page.
Conducting a Detailed Energy Audit
A structured energy audit highlights where you can realise the greatest gains from your heating system upgrade.
Metering and Monitoring
Install temporary sub-meters on boiler fuel, electricity for pumps and circulation losses. Monitoring over a full heating season yields data to benchmark against post-upgrade performance.
Identifying Heat Losses
Check building fabric (walls, windows, roofs) alongside pipework insulation. Heat lost through poorly lagged distribution can account for up to 20 per cent of consumption.
Pinpointing Operational Inefficiencies
Review control strategies, pump scheduling and thermostat setbacks. Often, outdated control sequences leave systems running unnecessarily during unoccupied hours.
Choosing the Right Replacement Technology
Your selection of boiler, pump and control technologies should align with your building’s profile, usage patterns and sustainability goals.
High-Efficiency Boilers
- Condensing boilers from brands like Vaillant and Remeha can deliver up to 98 per cent efficiency by reclaiming latent heat from flue gases.
- Biomass boilers suit premises with heavy, continuous loads and access to sustainable fuel sources.
Heat Pumps and Renewable Integration
- Air-source and ground-source heat pumps extract ambient energy with coefficients of performance (CoP) of 3–4:1, dramatically reducing fossil fuel use.
- Solar thermal panels preheat make-up water, lightening the load on boilers. Explore solutions from Andrews and Ebara.
Pump Selection and Distribution
- Replace fixed-speed pumps with variable-speed drives or EC pumps from Grundfos or Wilo to match flow to demand.
- Ensure you choose appropriately sized pumps from our commercial circulators range to avoid excess electrical consumption.
Designing for Optimal Control
Modern control systems transform standalone boilers into intelligent, responsive installations.
Zoning and Individual Room Control
Divide your building into multiple heating zones, offices, meeting rooms, warehouse and reception, and equip each with smart thermostats and Thermostatic Radiator Valves (TRVs). This prevents overheating unused areas and maximises occupant comfort.
Building Management System (BMS) Integration
Large sites benefit from a centralised BMS, which can:
- Automate temperature setbacks out of hours
- Monitor system alarms and performance trends
- Optimise multi-fuel integration (e.g. boiler plus heat pump)
Financial Planning and Return on Investment
A robust business case for your heating system upgrade ensures clarity on payback periods and net savings.
Calculating Lifecycle Costs
Factor in:
- Capital expenditure (equipment, installation)
- Operating costs (fuel, electricity, maintenance)
- Residual value (expected lifespan and resale potential)
Exploring Incentives and Grants
UK businesses may qualify for grants or zero-interest loans under schemes such as the Energy Technology List (ETL) or regional clean-growth programmes. Check local authority offerings or consult our team for guidance.
Forecasting Payback Period
With modern condensing boilers and efficient controls, typical ROIS range from 3–7 years, depending on fuel prices and usage patterns. A tailored energy audit will refine these estimates.
Compliance with Regulations and Standards
Your upgrade must meet current regulations to ensure safety, performance and future-proof compliance.
Building Regulations
- Part L standards set minimum energy performance requirements for commercial premises.
- Adequate flue clearances, accessible service spaces and documented commissioning are mandatory.
F-Gas and Refrigerant Controls
If integrating heat pumps, ensure refrigerant handling complies with F-Gas regulations. Work with certified installers to avoid fines.
Water Treatment and Legionella Risks
Upgraded systems must include chemical dosing and filtration. Devices from Flamco and Reflex maintain safe water quality.
Plantroom Layout and Space Optimisation
Efficient space utilisation reduces installation complexity and maximises service access.
Modular and Compact Equipment
Rooftop or wall-hung boilers, such as those in our central heating section, free floor space. Plate heat exchangers can also reduce footprint.
Accessibility for Servicing
Allow clearances of at least 600 mm around key components (boiler, pumps, valves). Group control panels at eye level and provide adequate lighting.
Ventilation and Safety
Ensure compliant air supply and extract routes. Oversized plantrooms can hamper airflow, while cramped spaces risk overheating and complicate routine maintenance.
Commissioning, Testing and Handover
A meticulous commissioning process is vital to verify that system performance matches design parameters.
Factory and Site Acceptance Tests
- Hydrostatic tests to check for leaks
- Burner tuning and flue emissions analysis
- Pump curve verification to confirm flow rates
Handover Documentation
Provide comprehensive manuals, as-fitted drawings and maintenance schedules. Arrange a formal handover meeting to walk through controls and emergency procedures.
Training, Aftercare and Maintenance Plans
A successful heating system upgrade extends beyond installation; ongoing care sustains peak performance.
Operator Training
Ensure your facility managers know how to:
- Adjust schedules and set-points
- Bleed and balance radiators
- Recognise alarm indications
Preventative Maintenance Contracts
Tailored plans from National Pumps and Boilers include:
- Annual boiler service and safety inspection
- Mid-season system health checks
- Priority breakdown support
Explore our full range of maintenance services on the homepage.
Performance Monitoring and Optimisation
Install remote monitoring to receive alerts on unusual behaviour, such as pump overload or rapid pressure changes, and intervene before failures occur.
Future-Proofing and Scalability
Plan upgrades that accommodate future growth and emerging technologies.
Modular Heat Generation
Consider installing additional connection points for extra boilers or heat pumps, allowing capacity expansion without major upheaval.
Digital Twins and Analytics
Create a digital replica of your HVAC system for virtual testing of control strategies and predictive maintenance modelling.
Renewable Hybridisation
Leave space and electrical capacity to add solar PV, battery storage or hydrogen-ready boilers as these technologies mature.
Why Choose National Pumps and Boilers?
At National Pumps and Boilers, we combine industry-leading expertise with a comprehensive product portfolio, from shower pumps to pressurisation units. Our accredited engineers tailor each heating system upgrade to your unique requirements, ensuring compliance, efficiency and longevity.
- Bespoke surveys and energy audits
- Project management from design through to commissioning
- Flexible finance options, including grant application support
- Ongoing maintenance and rapid response services
Ready to upgrade central heating in your commercial building? Contact us today via our contact page or explore our solutions on the homepage to take the next step towards a smarter, more efficient heating system.